Buckling-based low-voltage large-deformation micro-driver
A micro-actuator and large-deformation technology, applied in the field of micro-mechanics, can solve the problems such as the inability of the cantilever beam to achieve post-buckling symmetrical deformation, increase the fracture risk of the cantilever beam, and the disturbance in the horizontal direction, so as to avoid secondary buckling deformation, low cost, and buckling deformation. symmetrical effect
- Summary
- Abstract
- Description
- Claims
- Application Information
AI Technical Summary
Problems solved by technology
Method used
Image
Examples
Embodiment Construction
[0028] The buckling-based low-voltage large-deformation micro-actuator of the present invention uses micro-mechanical technology to release the extrusion potential energy stored in the assembly to the large deformation, fast response and sudden jump characteristics shown in the driving deformation, breaking through the tradition that the elastic force is the resistance The idea is to transform the elastic force into the main driving force, so as to realize the design purpose of small driving voltage, large driving displacement and small response time.
[0029] refer to image 3 , the whole driver is mainly made up of fixed base 38, micro-beam 34, outer frame 37. Wherein the material of the outer frame 37 is silicon, and an upper top cover 40 and a lower bottom cover 39 are fixed at both ends. The inner sides of the upper top cover 40 and the lower bottom cover 39 are 14.9 mm long, and gold films are deposited on their inner wall surfaces. The material of fixed base 38 is sili...
PUM
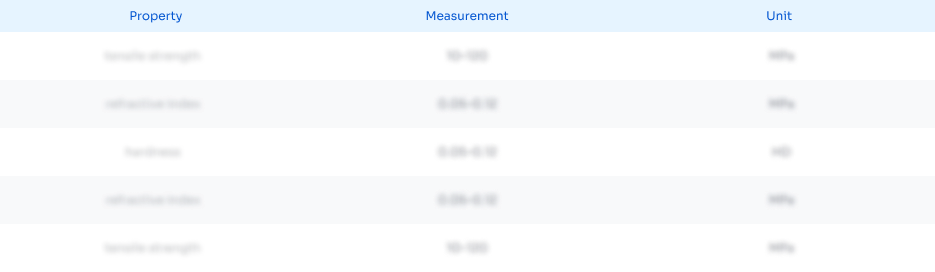
Abstract
Description
Claims
Application Information

- R&D
- Intellectual Property
- Life Sciences
- Materials
- Tech Scout
- Unparalleled Data Quality
- Higher Quality Content
- 60% Fewer Hallucinations
Browse by: Latest US Patents, China's latest patents, Technical Efficacy Thesaurus, Application Domain, Technology Topic, Popular Technical Reports.
© 2025 PatSnap. All rights reserved.Legal|Privacy policy|Modern Slavery Act Transparency Statement|Sitemap|About US| Contact US: help@patsnap.com