Preparation method of zinc oxide pressure-sensitive ceramic slurry and pressure-sensitive ceramic resistor material
A technology for pressure-sensitive ceramics and resistance materials, applied in the field of functional ceramic material manufacturing, can solve the problems of easy precipitation of slurry, uniform composition of difficult slurry, complicated process, etc., and achieve narrow particle size distribution range, uniform and stable slurry, and preparation Simple process effect
- Summary
- Abstract
- Description
- Claims
- Application Information
AI Technical Summary
Problems solved by technology
Method used
Image
Examples
Embodiment 1
[0034] Weigh the raw materials including the following molar percentages, ZnO: 95%, Bi 2 o 3 : 0.6%, Sb 2 o 3 : 0.9%, Co 2 o 3 : 1.0%, MnCO 3 : 0.5%, Cr 2 o 3 : 0.5%, NiO: 0.5%, SiO 2 : 1.0%, of which ZnO is the main raw material, except for ZnO, other raw materials are additives.
[0035] Pour the additive in the above ratio into a stirring ball mill, add pure water whose weight is 70% of the total weight of the additive, and ball mill for 1 hour until the particle size is less than 1.5 μm.
[0036] The mixing aid is weighed, and the mixing aid includes a dispersant and an antifoaming agent, and the weight percentages of the dispersing agent and the antifoaming agent in the entire slurry system are 0.2% and 0.03%, respectively. The dispersant is composed of ammonium tetradecyl acetate and polyethylene glycol (PEG4000), and the weight ratio of the ammonium tetradecyl acetate to the polyethylene glycol (PEG4000) is 1.8:1. The foaming agent is composed of tributyl phos...
Embodiment 2
[0040] Weigh the raw materials containing the following molar percentages, ZnO: 94.5%, Bi 2 o 3 : 0.6%, Sb 2 o 3 : 1.0%, Co 2 o 3 : 1.0%, MnCO 3 : 0.6%, Cr 2 o 3 : 0.5%, NiO: 0.5%, SiO 2 : 1.3%, of which ZnO is the main raw material, except for ZnO, other materials are additives.
[0041] The mixing aid is weighed, and the mixing aid includes a dispersant and an antifoaming agent, and the weight percentages of the dispersing agent and the antifoaming agent in the entire slurry system are 0.25% and 0.04%, respectively. The dispersant is composed of ammonium tetradecyl acetate and polyethylene glycol (PEG4000), and the weight ratio of the ammonium tetradecyl acetate to the polyethylene glycol (PEG4000) is 1.9:1. The foaming agent is composed of tributyl phosphate and water-soluble silicone oil in a weight ratio of 1.7:1.
[0042] Pour the additive in the above ratio into a stirring ball mill, add pure water whose weight is 90% of the total weight of the additive, and b...
Embodiment 3
[0045] Weigh the raw materials including the following molar percentages, ZnO: 94.3%, Bi 2 o 3 : 0.7%, Sb 2 o 3 : 1.1%, Co 2 o 3 : 1.1%, MnCO 3 : 0.6%, Cr 2 o 3 : 0.6%, NiO: 0.6%, SiO 2 : 1.0%, of which ZnO is the main raw material, except for ZnO, other materials are additives.
[0046] The mixing aid is weighed, and the mixing aid includes a dispersant and an antifoaming agent, and the weight percentages of the dispersing agent and the antifoaming agent in the entire slurry system are 0.3% and 0.04%, respectively. The dispersant is composed of ammonium tetradecyl acetate and polyethylene glycol (PEG4000), and the weight ratio of the ammonium tetradecyl acetate to the polyethylene glycol (PEG4000) is 2.0:1. The foaming agent is composed of tributyl phosphate and water-soluble silicone oil in a weight ratio of 1.8:1.
[0047] Pour the additive in the above ratio into a stirring ball mill, add pure water whose weight is 80% of the total weight of the additive, and bal...
PUM
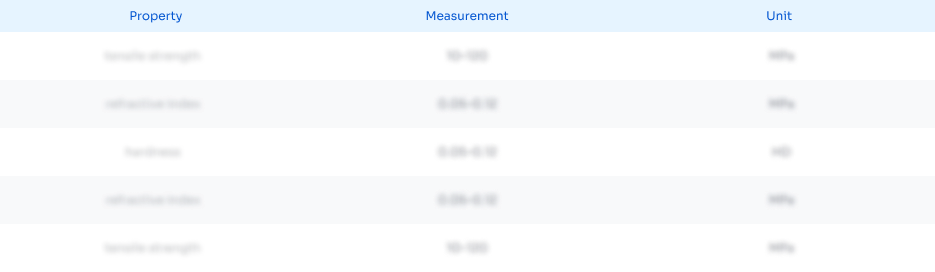
Abstract
Description
Claims
Application Information

- R&D
- Intellectual Property
- Life Sciences
- Materials
- Tech Scout
- Unparalleled Data Quality
- Higher Quality Content
- 60% Fewer Hallucinations
Browse by: Latest US Patents, China's latest patents, Technical Efficacy Thesaurus, Application Domain, Technology Topic, Popular Technical Reports.
© 2025 PatSnap. All rights reserved.Legal|Privacy policy|Modern Slavery Act Transparency Statement|Sitemap|About US| Contact US: help@patsnap.com