Processing method of tilted assembly angle bearing
A processing method and assembly angle technology, applied in the field of bearings, can solve the problems of unsatisfactory chamfer surface design, inconvenient assembly of motor shaft and bearing seat, etc., and achieve the effect of solving unsatisfactory chamfering
- Summary
- Abstract
- Description
- Claims
- Application Information
AI Technical Summary
Problems solved by technology
Method used
Image
Examples
Embodiment Construction
[0014] combine Figure 1 to Figure 3 , the present invention consists of an inner ring 1, an outer ring 2, a steel ball 3, a cage 4, and a dust cover 5, such as image 3 As shown, the X-axis direction refers to the axial direction of the bearing, and the Y-axis is on the plane where the end faces 7 of the inner and outer rings of the bearing are located. image 3 The radius of the arc 6 shown in is the same as figure 2 The radius R of the arc transition shown in is equal, R=0.4~0.6mm. The technological process of the present invention is basically the same as that of the known one, and the difference lies in that when the inner ring 1 and the outer ring 2 are cut, such as figure 2 As shown, the surface shape of the assembly chamfer is cut into an angle of 12-15° along the X-axis where the inner hole of the inner ring or the outer cylindrical surface is located, and is cut into an angle of 30-30° along the Y-axis where the end face of the inner ring and the end face of the ou...
PUM
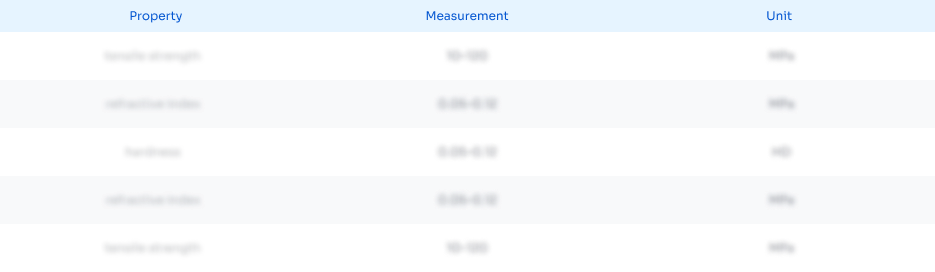
Abstract
Description
Claims
Application Information

- R&D Engineer
- R&D Manager
- IP Professional
- Industry Leading Data Capabilities
- Powerful AI technology
- Patent DNA Extraction
Browse by: Latest US Patents, China's latest patents, Technical Efficacy Thesaurus, Application Domain, Technology Topic, Popular Technical Reports.
© 2024 PatSnap. All rights reserved.Legal|Privacy policy|Modern Slavery Act Transparency Statement|Sitemap|About US| Contact US: help@patsnap.com