Method for controlling force telepresence of teleoperation robot based on tactile sensor
A tactile sensor and control method technology, applied in the control field, can solve the problems of limited accuracy of force sensor, inaccurate feedback force, inertial force and gravity interference, etc., to achieve the effect of improving control accuracy, broadening application scope and improving perception ability.
- Summary
- Abstract
- Description
- Claims
- Application Information
AI Technical Summary
Problems solved by technology
Method used
Image
Examples
Embodiment Construction
[0017] The teleoperated robot force sense telepresence control method includes: a main side loop 1 and a slave side loop 2, the main side loop 1 is composed of a main side loop switch 13, a main side controller 14, a master robot 12 and a comparator, and the slave side loop Loop 2 is composed of a slave controller 21, a slave robot 22 and a comparator. The specific operation steps are as follows:
[0018] The position difference signal x u Sent to the slave side controller 21, the slave side controller 21 adopts a proportional-integral controller and the output control quantity u formed by the slave side controller 21 s for where B s is the integral coefficient of the slave side controller, K s Be the proportional coefficient of the slave side controller, t is the amount of time, from the side controller 21 the described output control amount u s Output to slave robot 22 and be used for controlling from robot 22 motions, set tactile sensor 24 on slave robot 22 and describ...
PUM
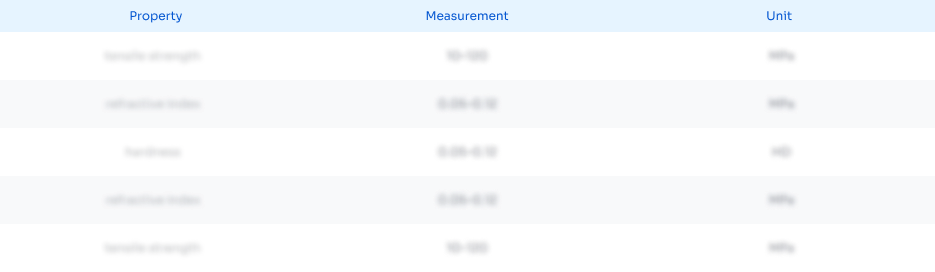
Abstract
Description
Claims
Application Information

- R&D
- Intellectual Property
- Life Sciences
- Materials
- Tech Scout
- Unparalleled Data Quality
- Higher Quality Content
- 60% Fewer Hallucinations
Browse by: Latest US Patents, China's latest patents, Technical Efficacy Thesaurus, Application Domain, Technology Topic, Popular Technical Reports.
© 2025 PatSnap. All rights reserved.Legal|Privacy policy|Modern Slavery Act Transparency Statement|Sitemap|About US| Contact US: help@patsnap.com