Automatic primer dipping and coating mechanism for plastic-coated spline shaft without sagging
A spline shaft and sagging technology, which is applied in the direction of coating, liquid coating device on the surface, surface pretreatment, etc., can solve the problems of uneven paint layer, reduce the bonding force of the plastic coating layer, waste, etc., and achieve the paint layer Uniformity and effect of improving dip coating efficiency
- Summary
- Abstract
- Description
- Claims
- Application Information
AI Technical Summary
Problems solved by technology
Method used
Image
Examples
Embodiment Construction
[0014] The present invention will be described in further detail below in conjunction with accompanying drawing
[0015] like figure 1 , figure 2 As shown, the non-sag dip coating primer mechanism of the present invention includes a machine room 1, a material basket 2, a material rack 3, a material feeding and discharging mechanism 4, a paint box 5, a paint box upgrading mechanism 6 and a hot air delivery mechanism 7; the machine room 1 It is a semi-enclosed machine room, with an exhaust device on the top, and a material inlet and outlet 101 on one side of the machine room; the material rack 3 is arranged outside the material inlet and outlet 101 of the machine room, and the material basket 2 is placed on the material rack 3. The basket is a frame structure, the spline shaft 8 to be dipped is hung upside down on the material basket, and the part of the spline shaft 8 to be dipped is facing downward; Pulling in and out of the machine room 1, the feeding and discharging mecha...
PUM
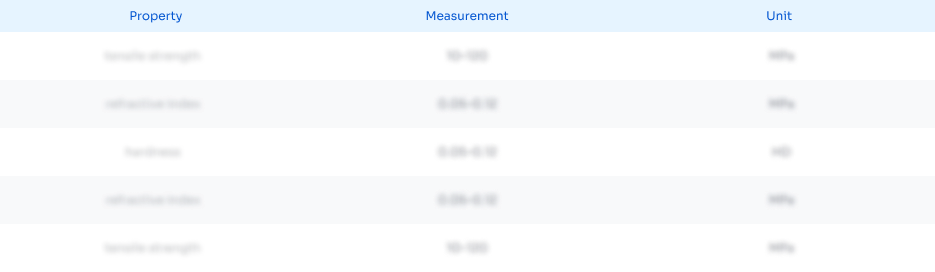
Abstract
Description
Claims
Application Information

- Generate Ideas
- Intellectual Property
- Life Sciences
- Materials
- Tech Scout
- Unparalleled Data Quality
- Higher Quality Content
- 60% Fewer Hallucinations
Browse by: Latest US Patents, China's latest patents, Technical Efficacy Thesaurus, Application Domain, Technology Topic, Popular Technical Reports.
© 2025 PatSnap. All rights reserved.Legal|Privacy policy|Modern Slavery Act Transparency Statement|Sitemap|About US| Contact US: help@patsnap.com