Electric steel insulating paint with high comprehensive performance
An insulating coating and comprehensive performance technology, applied in the direction of epoxy resin coating, coating, etc., can solve the problems of insufficient corrosion resistance of electrical steel substrates, corrosion of steel plate surfaces, and blistering of welds
- Summary
- Abstract
- Description
- Claims
- Application Information
AI Technical Summary
Problems solved by technology
Method used
Examples
Embodiment 1~7
[0019] In above-mentioned embodiment 1~7:
[0020] With 0.5mm thick non-oriented electrical steel plate as the substrate, apply the semi-organic electrical steel insulating coating of the composition shown in Examples 1 to 7 and Comparative Example with a grooved rubber roller coater, then bake at 350 ° C steel plate temperature 30s; cut out the sample plate to test the comprehensive performance of the coating (corrosion resistance, insulation, adhesion, punching property, weldability, etc.), and the test results are shown in Table 2.
[0021] Comprehensive performance of coating described in table 2 embodiment 1~7 and comparative example
[0022] Example number
[0023] Embodiment 1~7 illustrates: the coating described in embodiment 1~7 is light cyan color (partial white), and coating is complete, and all has good insulation, and interlayer resistance is all at 100Ω·mm 2 Above, weldability, heat resistance, punchability, adhesion are all good, and the comprehensive...
PUM
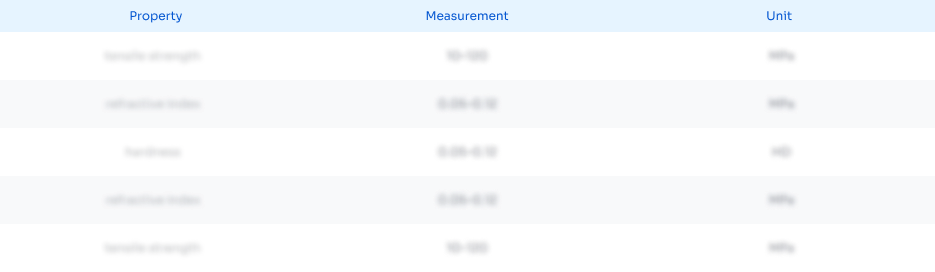
Abstract
Description
Claims
Application Information

- R&D Engineer
- R&D Manager
- IP Professional
- Industry Leading Data Capabilities
- Powerful AI technology
- Patent DNA Extraction
Browse by: Latest US Patents, China's latest patents, Technical Efficacy Thesaurus, Application Domain, Technology Topic, Popular Technical Reports.
© 2024 PatSnap. All rights reserved.Legal|Privacy policy|Modern Slavery Act Transparency Statement|Sitemap|About US| Contact US: help@patsnap.com