Continuous high vacuum rectification and purification method for lactide
A lactide and rectification technology, applied in continuous high vacuum distillation and purification of lactide, continuous high vacuum distillation, lactide purification field, can solve the problems of increasing equipment investment and operation difficulty, environmental pollution, etc. Achieve the effect of saving raw materials, reducing production costs, and making simple
- Summary
- Abstract
- Description
- Claims
- Application Information
AI Technical Summary
Problems solved by technology
Method used
Image
Examples
Embodiment 1
[0030] The diameter of the first rectification column is 400mm, filled with DN25 plum blossom flat ring packing, 12 theoretical plates, and the material is fed to the ninth block; the second rectification tower has a diameter of 300mm, filled with DN25 plum blossom flat ring packing, and 15 theoretical plates , feeding in the seventh block; the diameter of the third rectifying column is 500mm, filled with DN25 plum blossom flat ring packing, 8 theoretical plates, feeding in the sixth block. The processing capacity of the lactide crude liquid is 680kg / h, and the composition is 82% lactide, 9% water and lactic acid, 6% meso-lactide and 3% lactic acid oligomers, and the feed liquid temperature After mixing with the return material of the second rectification tower, it enters the ninth theoretical plate of the first rectification tower. The operating conditions of the tower are shown in Table 1, and the composition of the top and bottom materials is shown in Table 4. The bottom ma...
Embodiment 2
[0043] The lactide crude liquid treatment capacity is reduced to 600kg / h, and the composition is 85% lactide, 6.8% water and lactic acid, 6.5% meso-lactide and 1.7% lactic acid oligomers, other conditions With embodiment 1, operation result is shown in table 6 and table 7. The purity of lactide after refining reaches 99.52%, and the yield is 94.1%.
[0044] Table 6 The composition of the top and bottom materials of each tower when the treatment capacity is 600kg / h
[0045]
[0046] Note: The low boilers in Table 6 refer to water, lactic acid and meso-lactide.
[0047] Table 7 Feed to each tower and material flow at the top and bottom of the tower when the processing capacity is 600kg / h
[0048]
PUM
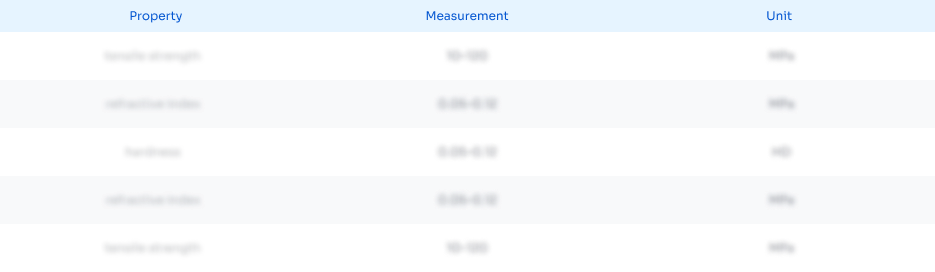
Abstract
Description
Claims
Application Information

- R&D
- Intellectual Property
- Life Sciences
- Materials
- Tech Scout
- Unparalleled Data Quality
- Higher Quality Content
- 60% Fewer Hallucinations
Browse by: Latest US Patents, China's latest patents, Technical Efficacy Thesaurus, Application Domain, Technology Topic, Popular Technical Reports.
© 2025 PatSnap. All rights reserved.Legal|Privacy policy|Modern Slavery Act Transparency Statement|Sitemap|About US| Contact US: help@patsnap.com