Universal rolling technology for rails
A universal rolling mill and universal technology, applied in the direction of metal rolling, etc., can solve the problems of good processing quality, uneven stress on rail-shaped rolled pieces, poor processing quality, etc., and achieve good processing quality, uniform force, and good symmetry Effect
- Summary
- Abstract
- Description
- Claims
- Application Information
AI Technical Summary
Problems solved by technology
Method used
Image
Examples
Embodiment 1
[0039] Depend on figure 1 , Figure 5 and Figure 7 As shown, after the rail-shaped rolling piece is rolled out from the pilot hole of BD area 1, before entering the universal area, it is turned over by the first turning device 2, and the waist 19 of the rail-shaped rolling piece becomes vertical, and the rail-shaped rolling piece The head 18 is positioned above the legs 20; then the overturned rail-shaped rolled piece enters the universal zone to carry out intermediate rolling and finish rolling through the vertical universal rolling mill and the vertical edger. During the rolling process in the universal zone, The waist 19 of the rail-shaped rolled piece is in a vertical state, the abdominal cavity 22 of the rail-shaped rolled piece is rolled by the left and right vertical rolls of the vertical universal rolling mill, and the head 18 of the rail-shaped rolled piece is supported by the left and right vertical rolls of the vertical universal rolling mill; Then the rail-shap...
Embodiment 2
[0041] Depend on figure 1 , Figure 5 and Figure 7 As shown, after the rail-shaped rolling piece is rolled out from the pilot hole of BD area 1, before entering the universal area, it is turned over by the first turning device 2, and the waist 19 of the rail-shaped rolling piece becomes vertical, and the rail-shaped rolling piece The head 18 is positioned above the legs 20; then the overturned rail-shaped rolled piece enters the universal zone to carry out intermediate rolling and finish rolling through the vertical universal rolling mill and the vertical edger. During the rolling process in the universal zone, The waist 19 of the rail-shaped rolled piece is in a vertical state, the abdominal cavity 22 of the rail-shaped rolled piece is rolled by the left and right vertical rolls of the vertical universal rolling mill, and the head 18 of the rail-shaped rolled piece is supported by the left and right vertical rolls of the vertical universal rolling mill; Before the rail-sh...
Embodiment 3
[0043] On the basis of Embodiment 1 or Embodiment 2, the pass pattern of the vertical universal rolling mill used for intermediate rolling in the universal area is formed by the upper and lower horizontal rolls and the left and right vertical rolls, and the vertical universal rolling mill used for intermediate rolling The ratio of the linear velocity of the lower horizontal roller to the linear velocity of the upper horizontal roller is 1.01-1.03. The ratio of the linear velocity of the lower horizontal roller to the linear velocity of the upper horizontal roller can be 1.01, 1.015, 1.02 or 1.03 and so on. When the roll diameters of the upper horizontal roll and the lower horizontal roll are the same, the rotational speed of the lower horizontal roll can be greater than that of the upper horizontal roll, so that the ratio of the linear speed of the lower horizontal roll to that of the upper horizontal roll is 1.01-1.03 Certainly, under the same situation of rotating speed, als...
PUM
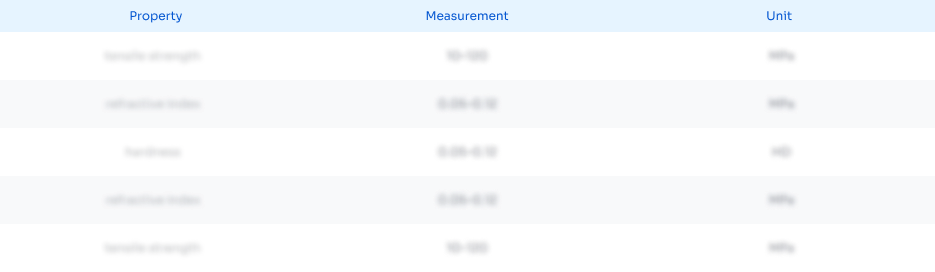
Abstract
Description
Claims
Application Information

- R&D
- Intellectual Property
- Life Sciences
- Materials
- Tech Scout
- Unparalleled Data Quality
- Higher Quality Content
- 60% Fewer Hallucinations
Browse by: Latest US Patents, China's latest patents, Technical Efficacy Thesaurus, Application Domain, Technology Topic, Popular Technical Reports.
© 2025 PatSnap. All rights reserved.Legal|Privacy policy|Modern Slavery Act Transparency Statement|Sitemap|About US| Contact US: help@patsnap.com