Composite material member with surface function layer and VIMP preparation method thereof
A composite material component and composite material technology, applied in the field of composite materials and their preparation, can solve the problems of not being able to impart a surface layer to the product, and achieve the effects of increasing stiffness, fast impregnation, and good surface quality
- Summary
- Abstract
- Description
- Claims
- Application Information
AI Technical Summary
Problems solved by technology
Method used
Image
Examples
Embodiment 1
[0040] Preparation of Composite Front Covers for Train Locomotives
[0041] Adopt preparation method of the present invention to prepare a kind of composite material head cover for locomotive, specifically comprise the following steps:
[0042] 1. Prepare the mold
[0043] According to the pre-designed locomotive head cover structure size prepared as follows image 3 Die 1 shown.
[0044] 2. Preparation of reinforced resin film by RFI process
[0045] 2.1 Cutting and laying reinforcing material: cutting the reinforcing material used to prepare the reinforced resin film. The reinforcing material is made of alkali-free glass fiber 02 plain cloth (purchased from Jiangsu Danyang Zhongya Glass Fiber Co., Ltd.), according to the shape and size of the mold 1 Cut three layers of E-glass fiber 02 plain weave, and then image 3 The surface layer fiber preform 2 is obtained by sequentially stacking and laying on the surface of the mold 1 as shown;
[0046] 2.2 The first resin system...
Embodiment 2
[0057] Preparation of Large FRP Composite Hull Shell
[0058] Adopt the preparation method of the present invention to prepare a kind of large-scale fiberglass composite material member used as the hull shell, specifically comprising the following steps:
[0059] 1. Prepare the mold
[0060] A single-sided rigid mold for molding is prepared according to the pre-designed structural size of the hull.
[0061] 2. Preparation of reinforced resin film by RFI process
[0062] 2.1 Cutting and laying reinforcing material: cutting the reinforcing material used to prepare the reinforced resin film, the reinforcing material is alkali-free glass fiber 02 plain cloth (purchased from Jiangsu Danyang Zhongya Glass Fiber Co., Ltd.), and cutting three times according to the shape and size of the mould. A layer of non-alkali glass fiber 02 plain weave cloth, and then stacked on the surface of the mold in turn;
[0063] 2.2 The first resin system for dip coating: prepare a certain amount of 9...
PUM
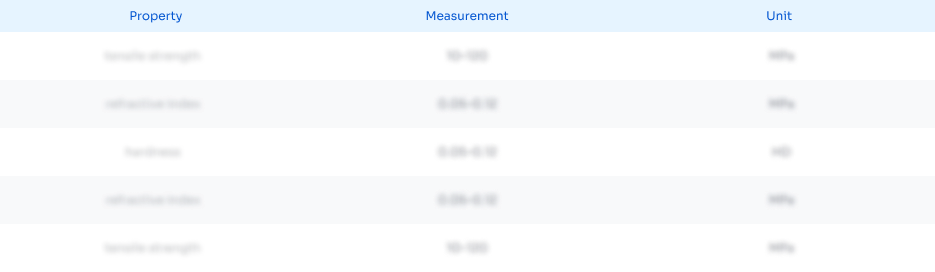
Abstract
Description
Claims
Application Information

- R&D
- Intellectual Property
- Life Sciences
- Materials
- Tech Scout
- Unparalleled Data Quality
- Higher Quality Content
- 60% Fewer Hallucinations
Browse by: Latest US Patents, China's latest patents, Technical Efficacy Thesaurus, Application Domain, Technology Topic, Popular Technical Reports.
© 2025 PatSnap. All rights reserved.Legal|Privacy policy|Modern Slavery Act Transparency Statement|Sitemap|About US| Contact US: help@patsnap.com