Automatic loading device for plates to be milled and loading material method thereof
An automatic feeding and milling technology, which is applied to wood processing equipment, mortising machines, slotting machines, etc., can solve the problems of waste of raw materials, unstable floor quality, etc., and achieve cost saving, manpower saving, and stable product quality Effect
- Summary
- Abstract
- Description
- Claims
- Application Information
AI Technical Summary
Problems solved by technology
Method used
Image
Examples
Embodiment 1
[0082] Use a forklift to move the tray with the semi-finished floor into the loading and unloading conveyor (1). There are forklift slots at the inlet and outlet of the loading and unloading conveyor. The forklift can directly place the pallet on the conveyor table. 2) In the original state, its table surface is slightly lower than the track surface of the loading and unloading conveyor, so that when the hydraulic lifting platform rises, it can jack up the tray. The loading and unloading conveyor adopts chain guide rails, (1) and (6) ends have forklift slots, and the pallet limit column is soft-started by frequency converter to prevent the impact displacement of the floor strips on the pallet. Then the hydraulic lifting steering table is started, and the pallet is jacked up so that the height of the uppermost slab is equal to the table surface of the transition roller table, and the lifting cylinder stops. At this time, the pusher (28) is started by a chain, and pushes the upp...
Embodiment 2
[0087] Use a forklift to move the tray with the semi-finished floor into the loading and unloading conveyor (1). There are forklift slots at the inlet and outlet of the loading and unloading conveyor. The forklift can directly place the pallet on the conveyor table. 2) In the original state, its table surface is slightly lower than the track surface of the loading and unloading conveyor, so that when the hydraulic lifting platform rises, it can jack up the tray. The loading and unloading conveyor adopts chain guide rails, and (1) (6) ends have forklift grooves to prevent the impact displacement of the floor strips on the pallet. Then the hydraulic lifting steering platform is started, and the pallet is lifted up so that the height of the uppermost slab can meet the height requirement of the suction plate sports car, the lifting cylinder stops, and then the suction plate sports car system starts, driven by the suction cup cylinder, the suction cup first descends , and then abso...
PUM
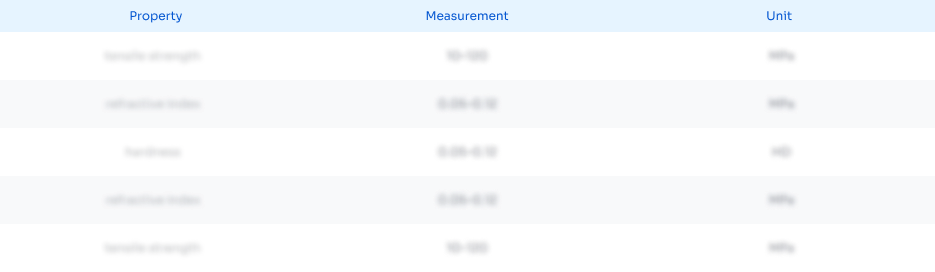
Abstract
Description
Claims
Application Information

- R&D
- Intellectual Property
- Life Sciences
- Materials
- Tech Scout
- Unparalleled Data Quality
- Higher Quality Content
- 60% Fewer Hallucinations
Browse by: Latest US Patents, China's latest patents, Technical Efficacy Thesaurus, Application Domain, Technology Topic, Popular Technical Reports.
© 2025 PatSnap. All rights reserved.Legal|Privacy policy|Modern Slavery Act Transparency Statement|Sitemap|About US| Contact US: help@patsnap.com