Manufacturing method of radiator
A manufacturing method and heat sink technology, applied to heat exchange equipment, etc., can solve the problems of increased manufacturing cost, labor and time consumption, and increased thermal conduction resistance, so as to simplify and speed up the manufacturing method, reduce assembly processes, and prevent thermal conduction resistance Effect
- Summary
- Abstract
- Description
- Claims
- Application Information
AI Technical Summary
Problems solved by technology
Method used
Image
Examples
Embodiment Construction
[0033] Such as figure 1 and figure 2 As shown, the present invention proposes a method for manufacturing a heat sink, which is used to automatically manufacture a heat sink that combines a metal substrate 1 and X heat dissipation fins 51, where X is a natural number, and the manufacturing method includes the following steps : a material preparation step S100, a alignment step S200, a punching step S300, a press bending step S400, a cutting and riveting step S500, a rotating step S600, repeated cutting and riveting steps S500 and rotating steps S600, and Once step S700 is taken out.
[0034] Please refer to image 3 The material preparation step S100 is to set the above-mentioned metal substrate 1 manually on a jig 40 of a positioning moving mechanism 30 on a processing machine 3, so that the metal substrate 1 is positioned on the jig 40, And the metal base plate 1 becomes a circular plate body, and the metal base plate 1 is made in the mode of stamping, and is punched with...
PUM
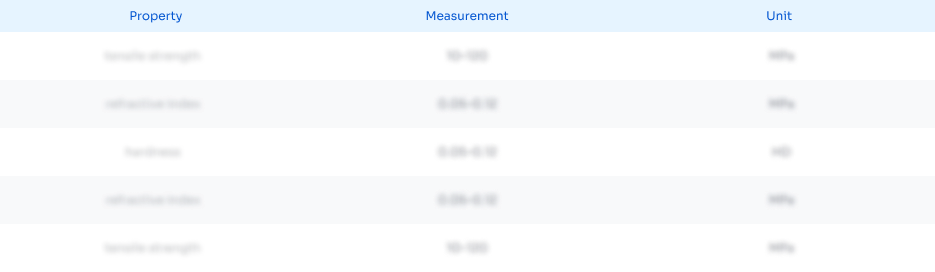
Abstract
Description
Claims
Application Information

- R&D
- Intellectual Property
- Life Sciences
- Materials
- Tech Scout
- Unparalleled Data Quality
- Higher Quality Content
- 60% Fewer Hallucinations
Browse by: Latest US Patents, China's latest patents, Technical Efficacy Thesaurus, Application Domain, Technology Topic, Popular Technical Reports.
© 2025 PatSnap. All rights reserved.Legal|Privacy policy|Modern Slavery Act Transparency Statement|Sitemap|About US| Contact US: help@patsnap.com