Submerged-arc welding process of large-size cylinder body
A technology for submerged arc welding and large cylinders, applied in welding equipment, welding equipment, arc welding equipment and other directions, can solve the problems of high labor intensity, low efficiency, and difficulty in ensuring product quality for welding workers, saving welding labor, improving The effect of product quality and high practical value
- Summary
- Abstract
- Description
- Claims
- Application Information
AI Technical Summary
Problems solved by technology
Method used
Image
Examples
Embodiment Construction
[0016] The present invention will be further described below in conjunction with the accompanying drawings and specific embodiments.
[0017] Such as figure 1 and figure 2 As shown, in the submerged arc welding process of large-scale cylinder, a reference operation platform 1 is first laid with steel plates on the construction site. On the reference operation platform 1, the processing of scribing, setting out, unfolding and splicing steel plates can be carried out, and the cylinder can also be processed. Correction and welding treatment, the size of the platform depends on the size of the cylinder made on site, usually 120m 2 Left and right, the problem of no reference on site can be solved by setting up a reference operating platform. Then, aiming at the difficulty of the butt weld of the cylinder body on site, a submerged arc welding bracket 2 for welding the cylinder body is set up on the reference operation platform 1, and an automatic welding operation table 3 is set ...
PUM
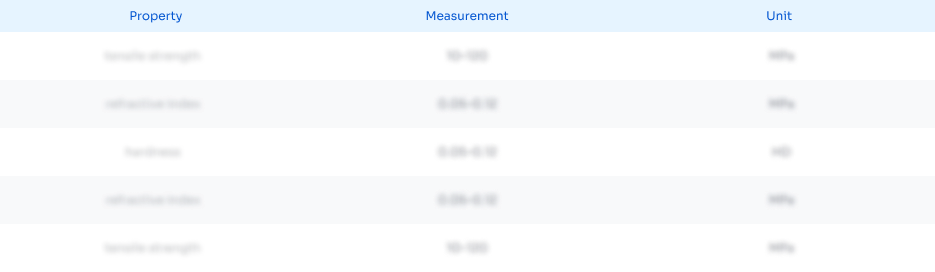
Abstract
Description
Claims
Application Information

- R&D
- Intellectual Property
- Life Sciences
- Materials
- Tech Scout
- Unparalleled Data Quality
- Higher Quality Content
- 60% Fewer Hallucinations
Browse by: Latest US Patents, China's latest patents, Technical Efficacy Thesaurus, Application Domain, Technology Topic, Popular Technical Reports.
© 2025 PatSnap. All rights reserved.Legal|Privacy policy|Modern Slavery Act Transparency Statement|Sitemap|About US| Contact US: help@patsnap.com