Recyclable sputtering target and manufacturing method thereof
A production method and technology of sputtering target, which are applied in sputtering coating, ion implantation coating, vacuum evaporation coating and other directions, can solve the problems of quality decline, inability to improve the quality of regenerated sputtering target material, etc., so as to reduce production cost , to avoid the effect of recycling and refining
- Summary
- Abstract
- Description
- Claims
- Application Information
AI Technical Summary
Problems solved by technology
Method used
Image
Examples
example 1
[0053] After cutting the back of the target containing ruthenium with a predetermined thickness (cutting), the surface of the target is sprayed with carbon dioxide (CO 2 Spraying) to remove microparticles or pollutants; the raw material powder with the same composition as the target material is subjected to a desorption process for ≤5 hours under high-temperature vacuum (800 ° C ~ 1200 ° C), and the target The material is put into a mold, and the above-mentioned raw material powder is covered in the sputtering corrosion surface groove (erosion groove) and above the sputtering corrosion surface and back to the periphery of the target, and pre-pressing (pre-pressing) and heating Press sintering (1200-1400° C.; 300-450 bar; 100-400 min) to obtain a finished regenerated sputtering target.
[0054] The sintering status of the general regenerated sputtering target and the regenerated sputtering target produced in Example 1 was detected by ultrasonic testing (UT).
[0055] Please r...
example 2
[0057] After carrying out wire cutting (wire cutting) with a predetermined thickness on the back of the return target containing ruthenium, the surface of the return target is cleaned by ultrasonic (ultrasonics) to remove particles or pollutants; The raw material powder with the same composition as the target is subjected to desorption (desorption) process within ≤5 hours under high temperature vacuum (800°C~1200°C), and the target is put into a mold, and the above powder is filled in the The sputtering corrosion surface groove (erosion groove) and the top of the sputtering corrosion surface and back to the periphery of the target, and pre-pressing (pre-pressing) and hot pressure sintering (1000 ~ 1500 ° C; 20000 ~ 35000 psi; 100 ~ 300min), a finished regenerated sputtering target can be obtained. It can then be tested by ultrasonic testing (UT).
example 3
[0059] After the Ruthenium (Ruthenium) is returned to the back of the target for cutting (cutting) with a predetermined thickness (predetermined thickness), the surface of the target is returned to the surface of the target for carbon dioxide supercritical fluid (CO 2 supercritical fluid) to remove microparticles or pollutants; after the raw material powder with the same composition as the target material is subjected to desorption (desorption) process at high temperature and vacuum (800 ° C ~ 1200 ° C) for ≤ 5 hours, and The back target is put into a mold, and the powder is filled in the sputtering corrosion surface groove (erosion groove) and the top of the sputtering erosion surface and the periphery of the back target, and pre-pressing (pre-pressing), Hot pressing (1200-1400°C; 300-450bar; 100-400min) and hot isobaric sintering (1000-1500°C; 20000-35000psi; 100-300min) to obtain a finished regenerated sputtering target. It can then be tested by ultrasonic testing (UT).
PUM
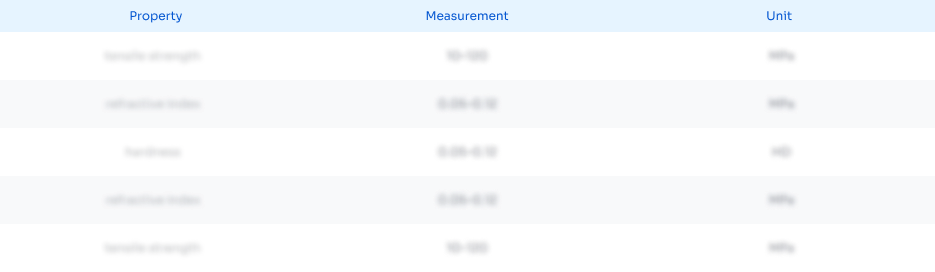
Abstract
Description
Claims
Application Information

- R&D
- Intellectual Property
- Life Sciences
- Materials
- Tech Scout
- Unparalleled Data Quality
- Higher Quality Content
- 60% Fewer Hallucinations
Browse by: Latest US Patents, China's latest patents, Technical Efficacy Thesaurus, Application Domain, Technology Topic, Popular Technical Reports.
© 2025 PatSnap. All rights reserved.Legal|Privacy policy|Modern Slavery Act Transparency Statement|Sitemap|About US| Contact US: help@patsnap.com