Directly-mixed rubber asphalt mixture and production method thereof
A technology for rubberized asphalt and mixture, which is applied in the field of rubberized asphalt mixture and production of rubberized asphalt mixture, can solve the problems of poor performance, affecting the thermal storage of the mixture, and low quality.
- Summary
- Abstract
- Description
- Claims
- Application Information
AI Technical Summary
Problems solved by technology
Method used
Image
Examples
Embodiment 1
[0016] The direct mix rubber asphalt mixture listed in this example is an AC10 graded urban white plus black mixture, which is configured according to the following weight ratio components: stone material: petroleum base asphalt: rubber powder modifier = 89:6:5 , the rubber powder modifier is composed of components in the following weight ratio: waste tire rubber powder: hexanediol = 100:3.
[0017] The direct mixing rubber asphalt mixture of the present embodiment is prepared according to the following method:
[0018] (1) Preparation of rubber powder modifier: Mix hexanediol into rubber powder in the weight ratio of rubber powder: hexanediol=100:3, mix and wet to obtain rubber powder modifier, and modify the rubber powder The agent is loaded into the powder bin of the mixing building for standby;
[0019] (2) Preparation of rubber asphalt mixture: heat the graded stone to 210-220°C in the mixing bin, and heat the petroleum-based asphalt to 160-170°C, according to the extrem...
Embodiment 2
[0021] The direct-mix rubber asphalt mixture listed in this example is AC13 primary road surface mixture, which is configured according to the following weight ratio components: stone material: petroleum base asphalt: rubber powder modifier = 92:5:3, so The rubber powder modifier is composed of components in the following weight ratio: waste tire rubber powder: hexanediol = 100:5.
[0022] The direct mixing rubber asphalt mixture of the present embodiment is prepared according to the following method:
[0023] (1) Preparation of rubber powder modifier: mix hexanediol into rubber powder in the weight ratio of rubber powder: hexanediol=100:5, mix and wet to obtain rubber powder modifier, and modify the rubber powder The agent is loaded into the powder bin of the mixing building for standby;
[0024] (2) Preparation of rubber asphalt mixture: heat the graded stone to 210-220°C in the mixing bin, and heat the petroleum-based asphalt to 160-170°C, according to the extreme mix of s...
Embodiment 3
[0026] The direct-mix rubber asphalt mixture listed in this example is AC16 intermediate layer mixture, which is configured according to the following weight ratio: stone material: petroleum base asphalt: rubber powder modifier = 94:4:2, the rubber The powder modifier is composed of components in the following weight ratio: waste tire rubber powder: hexanediol=100:7.
[0027] The direct mixing rubber asphalt mixture of the present embodiment is prepared according to the following method:
[0028] (1) Preparation of rubber powder modifier: Mix hexanediol into rubber powder according to the weight ratio of rubber powder: hexanediol=100:7, mix and wet to obtain rubber powder modifier, and modify the rubber powder The agent is loaded into the powder bin of the mixing building for standby;
[0029] (2) Preparation of rubber asphalt mixture: heat the graded stone to 210-220°C in the mixing bin, and heat the petroleum-based asphalt to 160-170°C, according to the extreme mix of stone...
PUM
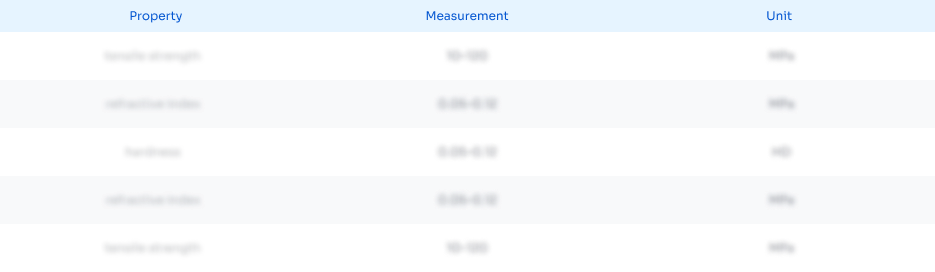
Abstract
Description
Claims
Application Information

- R&D Engineer
- R&D Manager
- IP Professional
- Industry Leading Data Capabilities
- Powerful AI technology
- Patent DNA Extraction
Browse by: Latest US Patents, China's latest patents, Technical Efficacy Thesaurus, Application Domain, Technology Topic, Popular Technical Reports.
© 2024 PatSnap. All rights reserved.Legal|Privacy policy|Modern Slavery Act Transparency Statement|Sitemap|About US| Contact US: help@patsnap.com