Combined reaction device
A combined reaction and equipment technology, applied in the field of catalytic reaction equipment, can solve the problems of increasing heat transfer temperature difference ΔT to enhance heat transfer, low reaction temperature, increase, decrease, etc.
- Summary
- Abstract
- Description
- Claims
- Application Information
AI Technical Summary
Problems solved by technology
Method used
Image
Examples
Embodiment 1
[0022] Embodiment 1: The combined reaction equipment of the present invention is used for methanol synthesis reaction, uses water as cooling medium, adopts image 3 The reaction device 9 shown is connected to steam drums 61,62. image 3 A solid valve means the valve is closed, and a hollow valve means the valve is open. The steam drum 62 connected to the heat exchange tube group 501 can be vaporized at a low pressure of 0.5-3 MPa, and the steam drum 61 connected to the heat exchange tube groups 502 and 503 can be vaporized at a pressure of 1-6 MPa. The reaction gas reacts from top to bottom in the catalyst layer 4, and the upper part has a high reaction speed and a large reaction heat, and can react at a temperature of 230-280°C. The reaction heat of the outer catalyst layer of 503 is small, and the reaction can be carried out at about 220-270°C. It can be seen that the heat transfer temperature difference inside and outside the heat exchange tube group 501 is several times ...
Embodiment 2
[0027] Embodiment 2: DME is produced with synthetic gas, and the methanol synthesis tower adopts figure 1 Horizontal water-cooling tower with a diameter of 4.0 meters and a built-in NC307 methanol catalyst 120M 3 , methanol dehydration tower to produce dimethyl ether, with a diameter of 3.0 meters and a built-in gamma-alumina methanol dehydration catalyst 50M 3 , the synthesis gas compressed to 9MPa is merged with the recycle gas, heated to 230°C and fed into the methanol synthesis tower, and the methanol synthesis reaction is carried out on the methanol catalyst layer at a temperature of about 250°C. The reaction heat is absorbed by the water in the horizontal water pipe in the synthesis tower to produce steam by-product, and the CH in the methanol synthesis tower gas is released. 3 The OH content is 21%. It is merged with the recovered methanol after rectification of the product dimethyl ether and enters the methanol dehydration reactor for dehydration to generate dimethyl ...
PUM
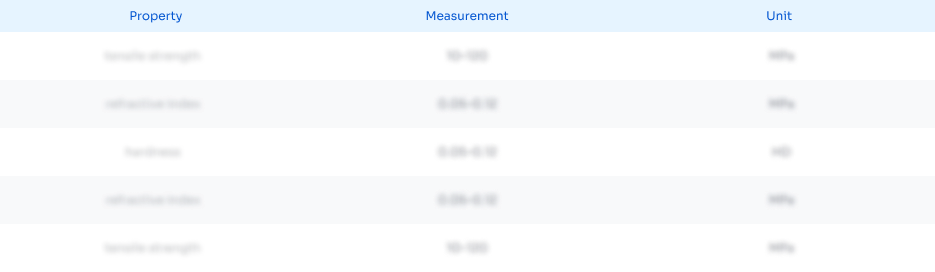
Abstract
Description
Claims
Application Information

- R&D
- Intellectual Property
- Life Sciences
- Materials
- Tech Scout
- Unparalleled Data Quality
- Higher Quality Content
- 60% Fewer Hallucinations
Browse by: Latest US Patents, China's latest patents, Technical Efficacy Thesaurus, Application Domain, Technology Topic, Popular Technical Reports.
© 2025 PatSnap. All rights reserved.Legal|Privacy policy|Modern Slavery Act Transparency Statement|Sitemap|About US| Contact US: help@patsnap.com