Forced internal recirculation type external cooler for catalytic cracking catalyst
A technology of catalytic cracking and external heat extraction, applied in the direction of fluidized bed heat exchanger, heat exchanger type, indirect heat exchanger, etc., can solve the problem of increasing the complexity and manufacturing difficulty of heat extraction equipment, and increasing the risk of difficult application of equipment , reduce the heat exchange efficiency of the heat pipe, etc., to achieve the effect of enhancing the flexibility of adjustment, easy manufacture and application, and simple structure
- Summary
- Abstract
- Description
- Claims
- Application Information
AI Technical Summary
Problems solved by technology
Method used
Image
Examples
Embodiment 1
[0040] See figure 1 As shown, the present embodiment provides a forced internal mixing type catalytic cracking catalyst external heat extractor 1, which comprises a round pot-shaped vertical shell 11 (inner diameter is D), and the upper part of the shell is provided with There is a catalyst inlet 111 and a gas outlet 112, and a catalyst outlet 113 is provided at the bottom. The interior of the shell forms the internal heat-taking space of the heat extractor, wherein: at the bottom of the heat extractor 1, there are two valves that can independently pass in fluidized gas and A gas distributor that can individually control the gas flow rate: a central gas distributor 12 arranged in the axial center area inside the heat extractor and a peripheral gas distributor 13 arranged in the side wall area; a gas distributor 12 inside the heat extractor 1 and 13 are provided with a plurality of vertically placed heat-taking pipes 14, and these heat-taking pipes 14 are evenly arranged in the...
Embodiment 2
[0043] See figure 2 As shown, this embodiment provides another form of a forced internal mixing type catalytic cracking catalyst external heat extractor 1. In the heat extractor and related operations of this embodiment, the structures and structures not specifically mentioned in the following description The operating conditions are the same as in Example One. The difference from the heat extractor described in Embodiment 1 is that in this embodiment, the central gas distributor 12 arranged at the bottom of the heat extractor 1 and arranged in the axial central area of the heat extractor and arranged on the side wall The peripheral gas distributors 13 of the zone are all annular pipe-type gas distributors, the diameter of the distribution ring of the central gas distributor 12 is (0.4-0.7) D, and the diameter of the distribution ring of the peripheral gas distributor 13 is (0.7-0.95) D, and the two The diameters of the distribution rings are different; the vertical distan...
Embodiment 3
[0045] See image 3 As shown, this embodiment provides a catalytic cracking device using the external heat extractor of the present invention as a catalytic cracking regenerant thermostat and a catalytic cracking method using the device. In the catalytic cracking unit of this embodiment, the regenerant thermostat adopts the heat extractor 1 described in Embodiment 1 or Embodiment 2 of the present invention (it can also be any other form of heat extractor of the present invention), and is arranged in The catalyst regenerator 2 and the catalytic cracking reactor of the catalytic cracking unit are between the riser reactor 3 in the figure, and the catalyst inlet 111 of the heat collector 1 is communicated with the regenerator 2, and the catalyst outlet 113 is communicated with the riser reactor 3 .
[0046] When utilizing this catalytic cracking device to carry out catalytic cracking, the hot regenerant flowing out from the catalyst regenerator 2 first enters in the heat extract...
PUM
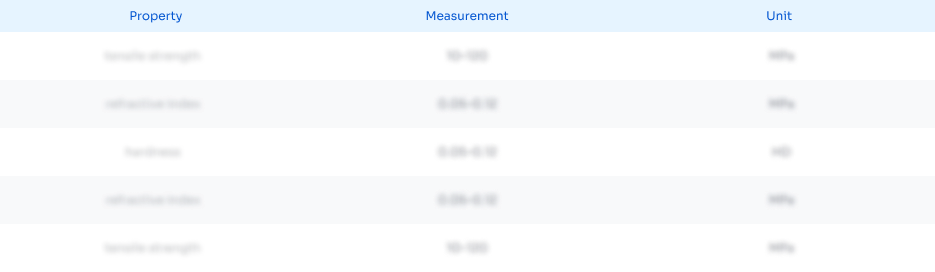
Abstract
Description
Claims
Application Information

- R&D
- Intellectual Property
- Life Sciences
- Materials
- Tech Scout
- Unparalleled Data Quality
- Higher Quality Content
- 60% Fewer Hallucinations
Browse by: Latest US Patents, China's latest patents, Technical Efficacy Thesaurus, Application Domain, Technology Topic, Popular Technical Reports.
© 2025 PatSnap. All rights reserved.Legal|Privacy policy|Modern Slavery Act Transparency Statement|Sitemap|About US| Contact US: help@patsnap.com