Heat treatment technology of ultra-long mandrel
A mandrel and super-long technology, applied in heat treatment furnaces, heat treatment equipment, manufacturing tools, etc., can solve the problems of expensive imported mandrels and long delivery cycles, and achieve low manufacturing costs, extended service life, and uniform heating Effect
- Summary
- Abstract
- Description
- Claims
- Application Information
AI Technical Summary
Problems solved by technology
Method used
Examples
Embodiment 1
[0022] Example 1: φ107×15000mm
[0023] On the intermediate frequency quenching furnace: (1) Power is supplied from the electrical operating platform, the heating coil, electrical appliances, and equipment cooling pump are turned on, the lead rod and mandrel are hung up, the drive wheel is started, and the coil is powered on after all the lead rods enter the coil; (2) Turn on the spray cooling water, and the mandrel moves forward closely with the lead rod; (3) Adjust the electrical parameters, heat up, and the quenching temperature is required to be 1020°C. The walking speed is 120mm / min. After passing a certain distance, the tail end of the workpiece is connected to another workpiece, and the two workpieces should be connected end to end. (4) After the workpiece is quenched, it is air-cooled. Then carry out a hardness test to ensure that the hardness is within the range of 57-62HRC.
[0024] On the intermediate frequency tempering furnace: (1) Power is supplied from the ele...
Embodiment 2
[0025] Example 2: φ180×18000mm
[0026] On the intermediate frequency quenching furnace: (1) Power is supplied from the electrical operating platform, the heating coil, electrical appliances, and equipment cooling pump are turned on, the lead rod and mandrel are hung up, the drive wheel is started, and the coil is powered on after all the lead rods enter the coil; (2) Turn on the spray cooling water, and the mandrel moves forward closely with the lead rod; (3) Adjust the electrical parameters, heat up, and the quenching temperature is required to be 1030°C. The walking speed is 110mm / min. After passing a certain distance, the tail end of the workpiece is connected to another workpiece, and the two workpieces should be connected end to end. (4) After the workpiece is quenched, it is air-cooled. Then carry out a hardness test to ensure that the hardness is within the range of 57-62HRC.
[0027] On the intermediate frequency tempering furnace: (1), the electrical operation plat...
Embodiment 3
[0028] Embodiment 3: φ277×20000mm
[0029] On the intermediate frequency quenching furnace: (1) Power is supplied from the electrical operating platform, the heating coil, electrical appliances, and equipment cooling pump are turned on, the lead rod and mandrel are hung up, the drive wheel is started, and the coil is powered on after all the lead rods enter the coil; (2) Turn on the spray cooling water, and the mandrel moves forward closely with the lead rod; (3) Adjust the electrical parameters, heat up, and the quenching temperature is required to be 1040°C. The walking speed is 100mm / min. After passing a certain distance, the tail end of the workpiece is connected to another workpiece, and the two workpieces should be connected end to end. (4) After the workpiece is quenched, it is air-cooled. Then carry out a hardness test to ensure that the hardness is within the range of 57-62HRC.
[0030] On the intermediate frequency tempering furnace: (1), the electrical operation p...
PUM
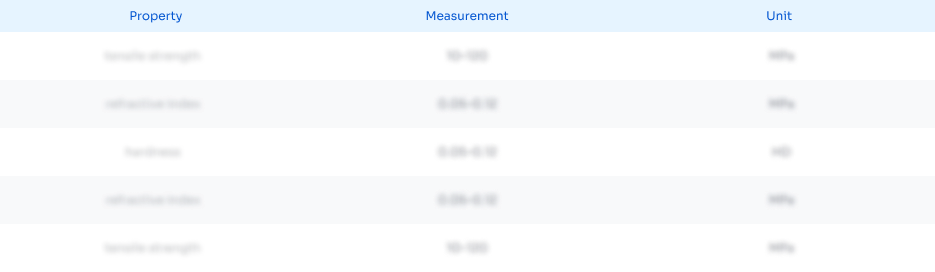
Abstract
Description
Claims
Application Information

- R&D
- Intellectual Property
- Life Sciences
- Materials
- Tech Scout
- Unparalleled Data Quality
- Higher Quality Content
- 60% Fewer Hallucinations
Browse by: Latest US Patents, China's latest patents, Technical Efficacy Thesaurus, Application Domain, Technology Topic, Popular Technical Reports.
© 2025 PatSnap. All rights reserved.Legal|Privacy policy|Modern Slavery Act Transparency Statement|Sitemap|About US| Contact US: help@patsnap.com