Backup roll reparation technique
A backup roller and process technology, applied in the field of backup roller repair technology, can solve the problems of increased cost, high carbon equivalent of bearing steel, difficult surfacing welding, etc., and achieve the effects of reducing processing costs, simple process steps, and ensuring uniformity
- Summary
- Abstract
- Description
- Claims
- Application Information
AI Technical Summary
Problems solved by technology
Method used
Examples
Embodiment Construction
[0006] The present invention will be described in more detail below by way of examples.
[0007] Process steps: a. Rough turning, φ500 rolls are turned to φ530, φ450 rolls are turned to φ430mm, and oil stains are removed; b. Preheating, 4 rolls are loaded into a trolley-type resistance furnace together, and the temperature is raised to 350 at a rate of 120 ° C per hour. ℃, keep warm for 8 hours and come out of the furnace, surfacing one by one, and the welded rolls are immediately sent into the furnace. 400°C; c. Overlay welding transition layer, roll preheated to 350°C, use φ3.2mm 306 welding wire + HJ431 flux to overlay the transition layer, bake the flux at 200-250°C for 2 hours before using, and degrease the welding wire After the rust, it can be wound into the welding wire reel; d. Surfacing hard surface layer, when the last roll has welded the transition layer and put it into the furnace, raise the temperature of the furnace to 380°C-400°C and keep it warm for 2 hours. ...
PUM
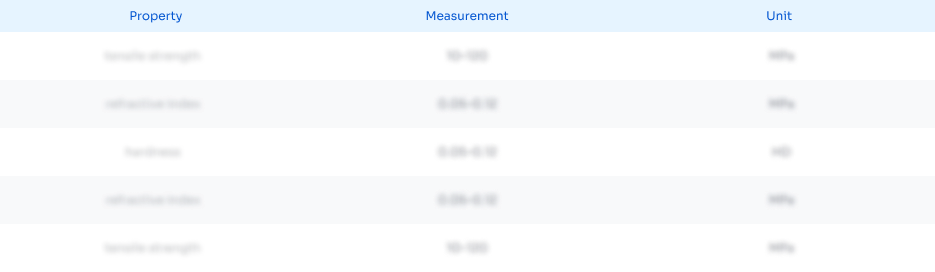
Abstract
Description
Claims
Application Information

- R&D Engineer
- R&D Manager
- IP Professional
- Industry Leading Data Capabilities
- Powerful AI technology
- Patent DNA Extraction
Browse by: Latest US Patents, China's latest patents, Technical Efficacy Thesaurus, Application Domain, Technology Topic, Popular Technical Reports.
© 2024 PatSnap. All rights reserved.Legal|Privacy policy|Modern Slavery Act Transparency Statement|Sitemap|About US| Contact US: help@patsnap.com