Method for solving blister generated in die-casting piece
A die-casting and bubble technology, which is applied in the field of solving the bubble generation in die-casting parts, can solve the problems of small gas generation and reduce the injection speed, and achieve the effect of reducing bubble defects.
- Summary
- Abstract
- Description
- Claims
- Application Information
AI Technical Summary
Problems solved by technology
Method used
Examples
Embodiment Construction
[0005] 1. Cool down the mold temperature to the working temperature.
[0006] 2. Reduce the injection speed to avoid airflow.
[0007] 3. Choose paint with small gas generation. The paint should be thin and uniform when used, and the mold should be closed after the thinner evaporates.
[0008] 4. Add overflow tank and exhaust tank, and pay attention to cleaning.
[0009] 5. Adjust the holding time of the mold.
[0010] 6. Trim the smelting process.
PUM
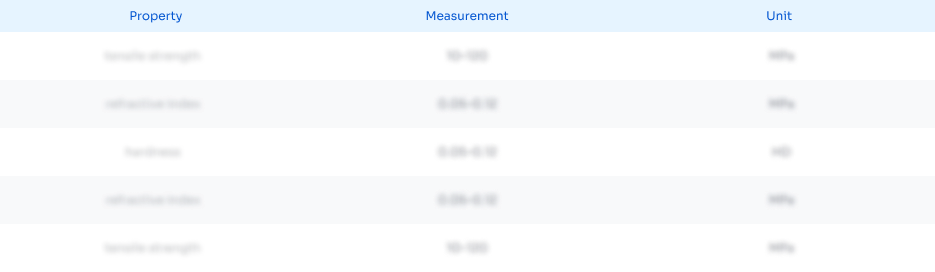
Abstract
Description
Claims
Application Information

- R&D
- Intellectual Property
- Life Sciences
- Materials
- Tech Scout
- Unparalleled Data Quality
- Higher Quality Content
- 60% Fewer Hallucinations
Browse by: Latest US Patents, China's latest patents, Technical Efficacy Thesaurus, Application Domain, Technology Topic, Popular Technical Reports.
© 2025 PatSnap. All rights reserved.Legal|Privacy policy|Modern Slavery Act Transparency Statement|Sitemap|About US| Contact US: help@patsnap.com