Centrifugal casting method for titanium alloy frame casting
A technology of centrifugal casting and titanium alloy, which is applied in the field of precision casting, and can solve problems such as complex calculation formulas and empirical formulas, shrinkage porosity, and low filling capacity
- Summary
- Abstract
- Description
- Claims
- Application Information
AI Technical Summary
Problems solved by technology
Method used
Image
Examples
Embodiment Construction
[0033] A centrifugal casting method for a titanium alloy frame casting, comprising shell preparation of the frame casting, furnace loading, calculation and determination of centrifugal pouring parameters, vacuum smelting pouring, and the like.
[0034] Base casting with mass mainly distributed on the outer ring figure 1 shown.
[0035] 1. The preparation of the base titanium alloy casting shell includes the following process steps:
[0036] 1. Use a rapid prototyping machine to make a wax mold of the base titanium alloy casting.
[0037] 2. Clean the base wax model with alcohol and let it dry naturally.
[0038] 3. Coat and hang the dried base wax model to make a shell, coat and hang 10 layers, and the interval between each layer of coating and hanging is 8 hours.
[0039] 4. After the shell making is completed, shell grinding is carried out, and then the shell is roasted for 8 hours at a roasting temperature of 1000°C.
[0040] 2. Furnace loading
[0041] 1. Smooth the f...
PUM
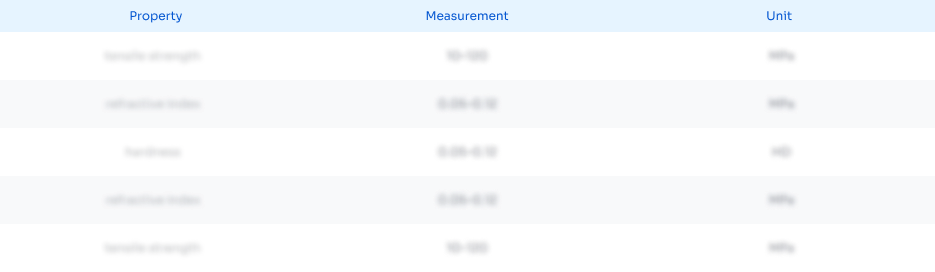
Abstract
Description
Claims
Application Information

- R&D
- Intellectual Property
- Life Sciences
- Materials
- Tech Scout
- Unparalleled Data Quality
- Higher Quality Content
- 60% Fewer Hallucinations
Browse by: Latest US Patents, China's latest patents, Technical Efficacy Thesaurus, Application Domain, Technology Topic, Popular Technical Reports.
© 2025 PatSnap. All rights reserved.Legal|Privacy policy|Modern Slavery Act Transparency Statement|Sitemap|About US| Contact US: help@patsnap.com