Online analysis method for turbonator shafting fatigue damage caused by subsynchronous oscillation
A subsynchronous oscillation, steam turbine generator technology, applied in mechanical bearing testing, engine testing, machine/structural component testing, etc. The effect of reducing error accumulation, improving solution accuracy, and improving analysis accuracy
- Summary
- Abstract
- Description
- Claims
- Application Information
AI Technical Summary
Problems solved by technology
Method used
Image
Examples
specific Embodiment approach
[0037] 1. Determine the parameters that characterize the subsynchronous oscillation of the power grid
[0038]There are many factors that cause the subsynchronous oscillation of the power grid and the unit. It is very important to select appropriate parameters to represent the subsynchronous oscillation amplitude of the machine network. In the present invention, the fluctuation values of the phase voltage and phase current of the generator actually measured by the power plant are used to represent the subsynchronous oscillation amplitude. The reasons for selecting this parameter are as follows: first, the factors that induce subsynchronous oscillation in the power grid may include various power electronic equipment, and it is not universal to use the parameters of these equipment to characterize the amplitude of subsynchronous oscillation; second, the generator speed difference It can effectively characterize the torsional vibration amplitude of the shaft system, but the acqu...
PUM
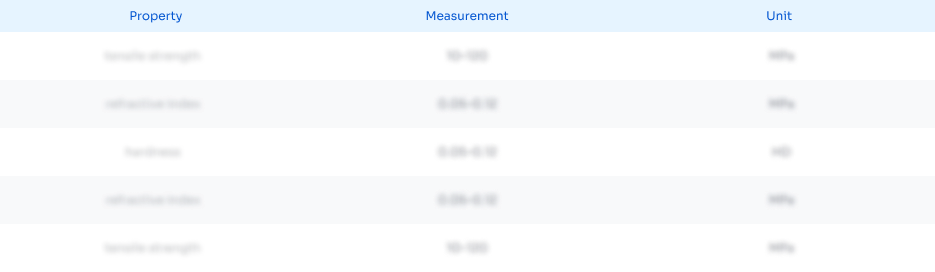
Abstract
Description
Claims
Application Information

- R&D Engineer
- R&D Manager
- IP Professional
- Industry Leading Data Capabilities
- Powerful AI technology
- Patent DNA Extraction
Browse by: Latest US Patents, China's latest patents, Technical Efficacy Thesaurus, Application Domain, Technology Topic, Popular Technical Reports.
© 2024 PatSnap. All rights reserved.Legal|Privacy policy|Modern Slavery Act Transparency Statement|Sitemap|About US| Contact US: help@patsnap.com