Method for avoiding blast-furnace gunning rebound materials mixing with cokes in hearth
A technology of blast furnace and coke, which is applied in the field of avoiding the mixing of blast furnace gunning rebound material and coke in the hearth, which can solve the problems of difficult cleaning, prolonging the blast furnace shutdown time, and taking a long time
- Summary
- Abstract
- Description
- Claims
- Application Information
AI Technical Summary
Problems solved by technology
Method used
Image
Examples
Embodiment Construction
[0010] 1. The material surface of the blast furnace is lowered to the tuyere belt. After the wind is stopped, 5 tons of coke is covered from the top of the blast furnace to the material surface (it can be increased or decreased according to the furnace capacity and the shape of the specific material surface), and then the staff enters the furnace to bring the material to the tuyere. Fill the surface depressions and flatten the top of the material surface as much as possible, and then spray a layer of covering agent on the material surface to keep it warm;
[0011] 2. Spread the iron plate on the covering agent and fix it. Specific method: the thickness of the iron plate is 0.5mm-0.8mm, it is rectangular, and the area of each piece is 2-3m 2 , Drill a number of round holes with a diameter of 2mm-3mm at the edge of the iron plate. Then penetrate the round holes of the adjacent iron plates into the iron wires and fix them so that there is no gap between the adjacent iron plate...
PUM
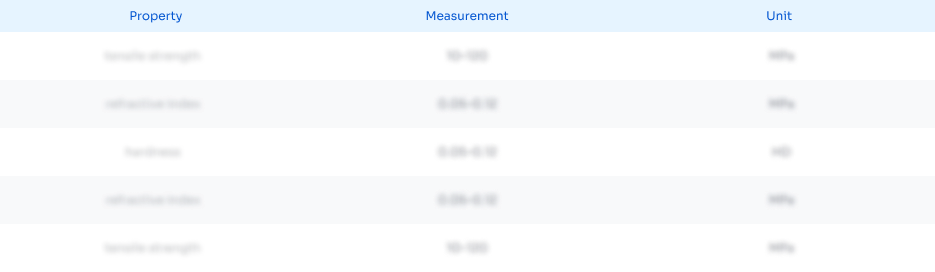
Abstract
Description
Claims
Application Information

- R&D Engineer
- R&D Manager
- IP Professional
- Industry Leading Data Capabilities
- Powerful AI technology
- Patent DNA Extraction
Browse by: Latest US Patents, China's latest patents, Technical Efficacy Thesaurus, Application Domain, Technology Topic, Popular Technical Reports.
© 2024 PatSnap. All rights reserved.Legal|Privacy policy|Modern Slavery Act Transparency Statement|Sitemap|About US| Contact US: help@patsnap.com