Pressure servo valve feedback mechanism
A servo valve and pressure technology, which is applied in the field of pressure servo valves, can solve the problems of affecting the valve output, the large output displacement of the nozzle, changing the pressure servo output pressure, etc., so as to improve the control performance and precision, stabilize the pressure output, and reduce the product cost. Effect
- Summary
- Abstract
- Description
- Claims
- Application Information
AI Technical Summary
Problems solved by technology
Method used
Image
Examples
Embodiment Construction
[0017] refer to figure 1 , 2 , 3. The feedback mechanism of the pressure servo valve includes a torque motor 1, a jet amplifier 2, a feedback mechanism 3 and a main valve 4; the torque motor 1 and the jet tube 21 are drivingly connected, and the receiver 22 of the jet amplifier 2 is pressed and fixed in the The control valve group 31 of the feedback mechanism 3, the torque motor 1 is fixed on the control valve group 31 of the feedback mechanism 3, the control valve group 31 is fixed on the main valve 4, the main valve 4 is a slide valve structure, and one side of the valve is respectively provided with The interface and flow channel connected with the control valve group 31 of the feedback mechanism 3 are respectively provided with the interface and flow channel connected with the oil supply, load, oil return and other system components on the other side.
[0018] The feedback mechanism 3 is a unique structure of the present invention, including a control valve group 31 and a...
PUM
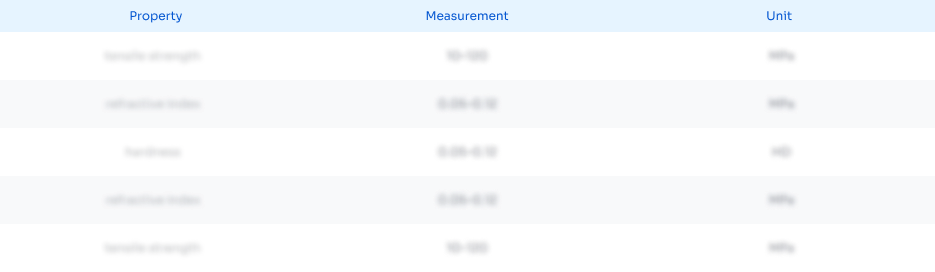
Abstract
Description
Claims
Application Information

- R&D
- Intellectual Property
- Life Sciences
- Materials
- Tech Scout
- Unparalleled Data Quality
- Higher Quality Content
- 60% Fewer Hallucinations
Browse by: Latest US Patents, China's latest patents, Technical Efficacy Thesaurus, Application Domain, Technology Topic, Popular Technical Reports.
© 2025 PatSnap. All rights reserved.Legal|Privacy policy|Modern Slavery Act Transparency Statement|Sitemap|About US| Contact US: help@patsnap.com