Hydraulic system and rotary drilling rig comprising same
A hydraulic system and hydraulic technology, applied in the field of rotary drilling rigs, can solve the problems of high pressure of the pressurized oil cylinder 140, the increase of the hydraulic oil of the pressurized oil cylinder 140, and the follow-up of load parts, so as to reduce power loss and improve the Overall efficiency, effect of avoiding overheating
- Summary
- Abstract
- Description
- Claims
- Application Information
AI Technical Summary
Problems solved by technology
Method used
Image
Examples
Embodiment 1
[0038] The hydraulic system provided in Embodiment 1 includes a main hydraulic circuit and an auxiliary hydraulic circuit. The main hydraulic circuit forms the power output part of the hydraulic system, and the auxiliary hydraulic circuit forms the control part of the hydraulic system to control the state of the main hydraulic circuit.
[0039] As shown in the figure, the main hydraulic circuit includes a hydraulic pump 3 , a pressurized oil cylinder 140 , and a reversing valve 9 . In this example, the hydraulic pump 3 is a load-sensing pump, which is driven to rotate by the engine 1 to output hydraulic power; the load-sensing pump includes a variable hydraulic pump 31 and a hydraulic compensation mechanism 32 for controlling the displacement of the variable hydraulic pump 31 . The main hydraulic circuit includes an oil supply pipeline 71 and a feedback pipeline 72, the oil supply pipeline 71 is connected between the oil supply port of the variable hydraulic pump 31 and the rev...
Embodiment 2
[0057] The working principle of the second embodiment is: when the pressurized oil cylinder 140 needs to be followed, the follow-up control valve 10 is placed in the left position, and the oil inlet port of the follow-up control overflow valve 11 communicates with the oil supply port of the hydraulic pump 3. , adjust the overflow pressure of the follow-up control overflow valve 11 so that the maximum pressure of the main oil pipeline 71 is equal to the overflow pressure, and the excess hydraulic oil flows back to the hydraulic oil tank through the follow-up control overflow valve 11; and the pressurized oil cylinder The force exerted by the power head 150 on the power head 150 is equal to the force exerted by the power head 150 on the piston of the pressurized oil cylinder 140 to maintain the force balance of the piston; the piston is stretched out at a predetermined speed; The downward moving speed of the head 150 remains equal, and the follow-up of the pressurized oil cylinde...
Embodiment 3
[0061] The working principle of the hydraulic system provided by Embodiment 3 is as follows:
[0062] When the rotary drilling rig provided with the hydraulic system in this example performs construction operations in uneven soil according to the CFA method mode, when the feed speed of the long helical drill rod 210 increases, the speed at which the power head 150 moves down also increases. , the pressure in the rodless chamber of the pressurized cylinder 140 will decrease; at this time, the controller obtains the information of the pressure change in the rodless chamber detected by the pressure sensor 12, and then determines the overflow pressure according to a predetermined strategy, and sends it to the follow-up control overflow. Flow valve 11 outputs a corresponding electric signal, so that the follow-up control overflow valve 11 adjusts its overflow pressure according to the corresponding electrical signal, so that the pressure at the induction port O of the hydraulic comp...
PUM
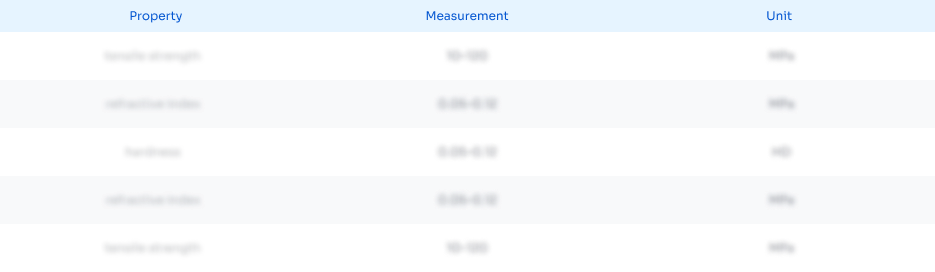
Abstract
Description
Claims
Application Information

- R&D
- Intellectual Property
- Life Sciences
- Materials
- Tech Scout
- Unparalleled Data Quality
- Higher Quality Content
- 60% Fewer Hallucinations
Browse by: Latest US Patents, China's latest patents, Technical Efficacy Thesaurus, Application Domain, Technology Topic, Popular Technical Reports.
© 2025 PatSnap. All rights reserved.Legal|Privacy policy|Modern Slavery Act Transparency Statement|Sitemap|About US| Contact US: help@patsnap.com