Paper chopping blade and machining method thereof
A processing method and technology of blades, which are applied to knives, grain processing, household appliances, etc., can solve the problems of cumbersome processing of shredder blades, poor assembly precision of paper shredder knives, and high cost of energy strip steel, and achieve low cost and small size. Precise, productive results
- Summary
- Abstract
- Description
- Claims
- Application Information
AI Technical Summary
Problems solved by technology
Method used
Image
Examples
Embodiment Construction
[0021] Embodiments of the present invention will now be described with reference to the drawings, in which like reference numerals represent like elements.
[0022] refer to Figure 1-2 , is a perspective view of a shredding blade 1 produced by the processing method of the shredding blade of the present invention, the shredding blade 1 includes a blade body 10, an installation hole 11 in the center of the blade body 10, a knife edge positioned at the periphery of the blade body 12 and a knife tip 13 protruding outward from the periphery of the knife body, the area between the knife edge 12 and the mounting hole 11 on the outer surface of the knife body 10 is provided with a concave ring 14, and the outer surface of the other side of the knife body 10 The area between the knife edge 12 and the mounting hole 11 is correspondingly provided with a protruding ring 15 .
[0023] refer to image 3 , the processing method of shredder blade 1 of the present invention, comprises the f...
PUM
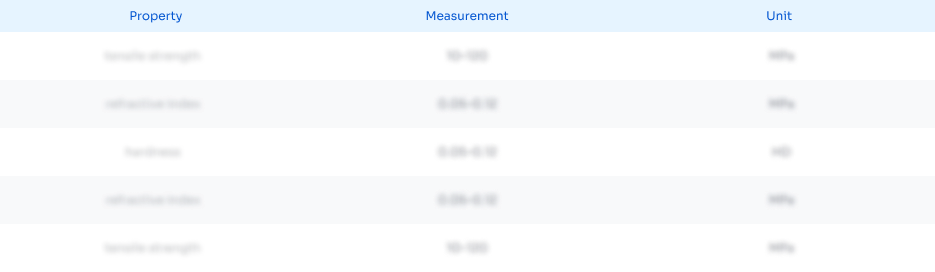
Abstract
Description
Claims
Application Information

- Generate Ideas
- Intellectual Property
- Life Sciences
- Materials
- Tech Scout
- Unparalleled Data Quality
- Higher Quality Content
- 60% Fewer Hallucinations
Browse by: Latest US Patents, China's latest patents, Technical Efficacy Thesaurus, Application Domain, Technology Topic, Popular Technical Reports.
© 2025 PatSnap. All rights reserved.Legal|Privacy policy|Modern Slavery Act Transparency Statement|Sitemap|About US| Contact US: help@patsnap.com