Exhaust gas fume afterheat recovering system with heat-accumulating and temperature-equalizing equipment
A waste heat recovery system and flue gas waste heat technology are applied in the fields of treatment, waste heat recovery, and flue gas dust removal. It can solve the problems of large horse-drawn carts and low steam production, and achieve the effects of improving efficiency, reducing investment, and reducing the amount of mixed cold air.
- Summary
- Abstract
- Description
- Claims
- Application Information
AI Technical Summary
Problems solved by technology
Method used
Image
Examples
Embodiment 1
[0026] Such as figure 1 As shown, the waste heat recovery system in this embodiment includes a settling chamber 3, heat storage and temperature equalization equipment 4, waste heat recovery device 5 and dust collector 6 arranged in sequence, wherein the heat storage and temperature uniformity equipment 4 is set in the settling chamber 3 and the waste heat recovery device 5, the heat storage uniform temperature equipment 4 includes a flue gas inlet 41, a heat storage body 42, a dust removal device 43, a flue gas outlet 44 and an ash hopper 45, and the heat storage body 42 is arranged on the flue gas Between the gas inlet 41 and the flue gas outlet 44, the arrangement is vertical or horizontal; the ash removal device 43 is arranged between the regenerators 42 in sections; the flue gas inlet 41 and the flue gas The outlet 44 is respectively connected with the flue gas outlet 32 of the settling chamber 3 and the flue gas inlet 51 of the waste heat recovery device 5 .
Embodiment 2
[0028] Such as figure 2 As shown, the difference between this embodiment and Embodiment 1 is that the heat storage uniform temperature equipment 4 is arranged in the settling chamber 3, and is integrated with the settling chamber to form a heat storage uniform temperature settling chamber. The warm settling chamber includes a flue gas inlet 31, a settling flue 33, a heat storage body 42, a dust removal device 43, a flue gas outlet 34 (44), and a dust removal door 34, wherein the heat storage body 42 is arranged in the settling chamber 3 There are 34 flue gas outlets.
Embodiment 3
[0030] Such as image 3 As mentioned above, the difference between this embodiment and Embodiment 1 is that: the heat storage and uniform temperature equipment 4 is set in the waste heat recovery device 5, and is integrated with the waste heat recovery device 5 to form a heat storage and uniform temperature waste heat recovery device. The heat uniform temperature waste heat recovery device includes a flue gas inlet 41 (51), a heat storage body 42, a dust removal device 43, a heat exchanger 53, a flue gas outlet 52 and an ash hopper 45, wherein the heat storage body 4 is arranged on the waste heat The flue gas inlet 51 of the recovery device 5.
[0031] Of course, the present invention can also have other implementations, for example, the waste heat recovery device 5 can also be a flue gas cooling device.
[0032] When used, such as Figure 1-3 As shown, the high-temperature flue gas generated in the electric furnace 1 is heat-exchanged through the cooling water pipeline (her...
PUM
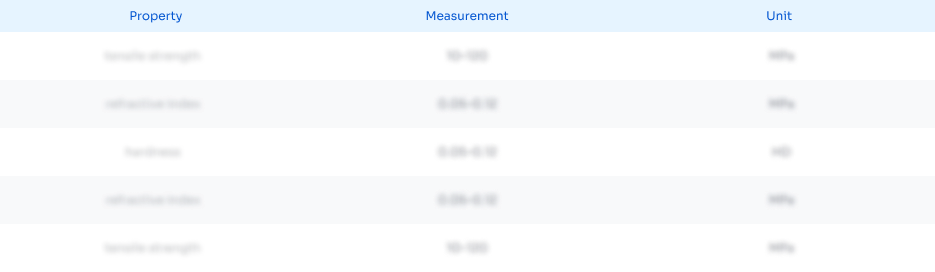
Abstract
Description
Claims
Application Information

- R&D
- Intellectual Property
- Life Sciences
- Materials
- Tech Scout
- Unparalleled Data Quality
- Higher Quality Content
- 60% Fewer Hallucinations
Browse by: Latest US Patents, China's latest patents, Technical Efficacy Thesaurus, Application Domain, Technology Topic, Popular Technical Reports.
© 2025 PatSnap. All rights reserved.Legal|Privacy policy|Modern Slavery Act Transparency Statement|Sitemap|About US| Contact US: help@patsnap.com