Method for removing impurities by oxidation in process of zinc hydrometallurgy
A technology of hydrometallurgy and secondary zinc oxide, which is applied in the direction of improving process efficiency, etc., can solve the problems of electro-zinc impurity removal and high product quality, and achieve smooth production, high product quality and cost reduction
- Summary
- Abstract
- Description
- Claims
- Application Information
AI Technical Summary
Problems solved by technology
Method used
Image
Examples
Embodiment 1
[0022] Pumped 40m in the sub-zinc oxide leach tank 3 Electrolytic waste solution (see Table 1 for composition), drop into 10 tons of zinc oxide (see Table 2 for composition), stir for 50min, until the pH is 4.0, add H2O with a mass percentage of 27.5% 2 o 2 Solution 270kg, make the Fe in the solution 2+ <1g / L, then add 150kg of lime to adjust the pH to 5.2, stir for 60min;
[0023] Table 1
[0024] Element
Zn
h 2 SO 4
Fe
As
Sb
Ge
co
Cu
Cd
F
content,
g / L
38
150
0.015
0.00006
0.00006
0.00007
0.0008
0.0003
0.002
0.15
[0025] Table 2
[0026]
[0027] table 3
[0028] Element
Zn
Fe
As
Sb
Ge
co
Cu
Cd
F
Content, g / L
132
0.6
0.0003
0.0004
0.0003
0.005
0.025
0.21
0.18
[0029] Pump the filtered leaching solutio...
Embodiment 2
[0039] Pumped 39m in the sub-zinc oxide leach tank 3 Electrolyzed waste solution (see Table 7 for composition), drop into 10 tons of zinc oxide (see Table 8 for composition), stir for 50min, until pH is 4.5, adding mass percent is 27.5% H 2 o 2 Solution 300kg, make the Fe in the solution 2+ <1g / L, then add 120kg of lime to adjust the pH to 5.2, stir for 60min;
[0040] Table 7
[0041] Element
Zn
h 2 SO 4
Fe
As
Sb
Ge
co
Cu
Cd
F
Content, g / L
42
149
0.016
0.00007
0.00005
0.00006
0.0009
0.0002
0.001
0.13
[0042] Table 8
[0043]
[0044] Table 9
[0045] Element
Zn
Fe
As
Sb
Ge
co
Cu
Cd
F
Content, g / L
136
0.8
0.0002
0.0003
0.0002
0.005
0.029
0.21
0.16
[0046] Pump the filtered leaching solution into the deep iron removal reaction tank, maintain the te...
Embodiment 3
[0056] Pumped 43m in the sub-zinc oxide leach tank 3 Electrolyzed waste liquid (composition sees Table 13), drops into 11 tons of zinc oxide (composition sees Table 14), stirs 50min, until pH is 3.5, adding mass percentage is 27.5% H 2 o 2 Solution 270kg, make the Fe in the solution 2+ <1g / L, then add 200kg of lime to adjust the pH to 5.0, stir for 60min;
[0057] Table 13
[0058] Element
Zn
h 2 SO 4
Fe
As
Sb
Ge
co
Cu
Cd
F
content,
g / L
38
149
0.015
0.00007
0.00005
0.00006
0.001
0.0001
0.001
0.15
[0059] Table 14
[0060]
[0061] Table 15
[0062]
Element
Zn
Fe
As
Sb
Ge
co
Cu
Cd
F
Content, g / L
131
0.7
0.0002
0.0004
0.0003
0.007
0.023
0.22
0.15
[0063] P...
PUM
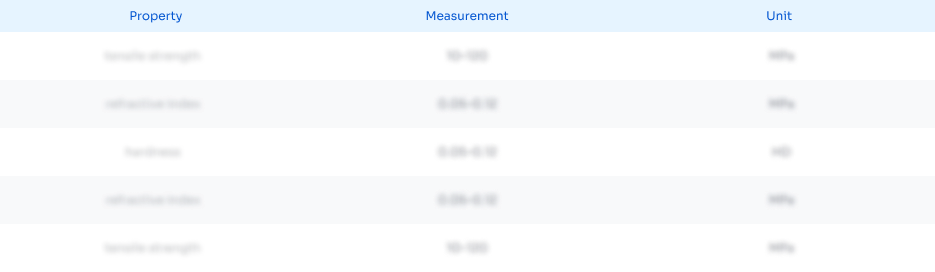
Abstract
Description
Claims
Application Information

- R&D
- Intellectual Property
- Life Sciences
- Materials
- Tech Scout
- Unparalleled Data Quality
- Higher Quality Content
- 60% Fewer Hallucinations
Browse by: Latest US Patents, China's latest patents, Technical Efficacy Thesaurus, Application Domain, Technology Topic, Popular Technical Reports.
© 2025 PatSnap. All rights reserved.Legal|Privacy policy|Modern Slavery Act Transparency Statement|Sitemap|About US| Contact US: help@patsnap.com