Method for preparing liquefied natural gas by using coke-oven gas
A technology of liquefied natural gas and coke oven gas, which is applied in the direction of gas fuel, petroleum industry, fuel, etc., can solve the problem of low energy consumption of liquefaction, achieve the effects of reduced cycle ratio, reduced consumption cost, and stable operation
- Summary
- Abstract
- Description
- Claims
- Application Information
AI Technical Summary
Problems solved by technology
Method used
Image
Examples
Embodiment 1
[0034] The cryogenic separation (rectification separation) flow process of the present embodiment is as follows:
[0035] Composition (%) (volume percent) of coke oven gas after methanation: H 2 35.1,N 2 5.9, CH 4 59. Air volume 10000Nm 3 / h, pressure 1.75MPa, temperature 40°C.
[0036] Its process is as follows figure 1 shown. 10000Nm 3 / h Methanated gas is pressurized to 3.0MPa, dehydrated and dried, then enters heat exchanger E1 through pipeline 1 and is cooled to -89°C, and passes through pipeline 4 as a heat source for rectification column reboiler R, and is cooled to - 98°C, enters the heat exchanger E2 through the pipeline 5, and is cooled to -150°C ~ -155°C by the negative pressure methane evaporation gas of the pipeline 15, the liquid methane of the pipeline 20, the hydrogen nitrogen expansion gas of the pipeline 10 and the hydrogen nitrogen gas of the pipeline 8, saving Flow to 2.5MPa into the rectifying tower T. The methane with a purity greater than 99....
Embodiment 2
[0040] The cryogenic separation (rectification separation) flow process of the present embodiment is as follows:
[0041] Composition (%) (volume percent) of coke oven gas after methanation: H 2 35.1,N 2 5.9, CH 4 59. Air volume 10000Nm 3 / h, pressure 1.75MPa, temperature 40°C.
[0042] Its process is as follows figure 2 shown. 10000Nm 3 / h The gas after methanation is pressurized to 3.0MPa, dehydrated and dried, then enters the heat exchanger E1 through the pipeline 1 and is cooled to -89°C, and passes through the pipeline 4 as a heating source for the reboiler R of the rectification tower, and is cooled to -98°C, enter the heat exchanger E2 from the pipeline 5 for further cooling, throttle to 2.5MPa through the pipeline 6, and enter the rectification tower T through the pipeline 7. Under the action of rectification, methane with a purity greater than 99.5% is obtained in the tower kettle, and the liquid methane in the tower kettle is throttled to 0.14MPa through ...
Embodiment 3
[0046] The liquefaction process of the present embodiment is as follows:
[0047] Its process is as follows image 3 shown. The methane 5729Nm that obtains by embodiment 1 3 / h enters compressor COM from pipeline 1, compresses to 0.35MPa, mixes with methane from pipeline 18 (mixed gas of methane after expansion and vaporized methane of V2) and enters the second stage of compressor, then pressurizes to 5.0MPa, and cools Then it enters the heat exchanger E1 from the pipeline 2, then enters the precooler E2 from the pipeline 3, cools down to -45°C, enters the heat exchanger E3 from the pipeline 4 for further cooling, throttles it to 3.0MPa from the pipeline 5, and enters it through the pipeline 6 In the gas-liquid separator V1, the uncondensed gas enters the heat exchanger E3 from the pipeline 13, is heated to -49°C, and enters the expander EXP through the pipeline 14. After expansion, the pressure is 0.4MPa, and the expanded gas is mixed with the gas from the pipeline 15 and t...
PUM
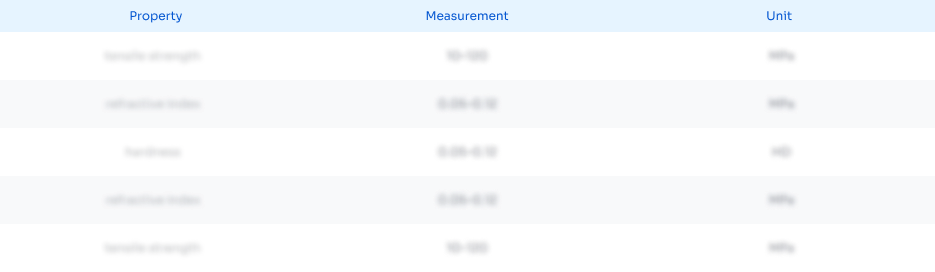
Abstract
Description
Claims
Application Information

- Generate Ideas
- Intellectual Property
- Life Sciences
- Materials
- Tech Scout
- Unparalleled Data Quality
- Higher Quality Content
- 60% Fewer Hallucinations
Browse by: Latest US Patents, China's latest patents, Technical Efficacy Thesaurus, Application Domain, Technology Topic, Popular Technical Reports.
© 2025 PatSnap. All rights reserved.Legal|Privacy policy|Modern Slavery Act Transparency Statement|Sitemap|About US| Contact US: help@patsnap.com