Rare earth-containing aluminum alloy used for semisolid state rheoforming and preparation method of semisolid state slurry thereof
A semi-solid rheological and semi-solid slurry technology, which is applied in the field of rare earth aluminum alloys for semi-solid rheological forming, can solve the problems of low roundness of the primary phase of the semi-solid structure and unfavorable semi-solid forming, and achieve a reduction in process Effects of cost control, fine spherical particles, and reduced control accuracy
- Summary
- Abstract
- Description
- Claims
- Application Information
AI Technical Summary
Problems solved by technology
Method used
Image
Examples
Embodiment 1
[0020] Embodiment 1: First, 631.7 g of high-purity aluminum (purity is 99.99%) and 838.4 g of Al-12% Si master alloy are added in a graphite clay crucible, and the alloy is melted in a resistance furnace at a melting temperature of 750° C. After the metal is completely melted, press 6.4g of pure Mg (99.9% purity) into the metal melt with a bell jar, and the alloy is heated at 720°C with C 2 Cl 6 Degassing and refining. After standing for 20 minutes, raise the temperature to 750°C and add 25Al-6% Er intermediate alloy. Use a K-type thermocouple to monitor the temperature of the molten metal. Lower the temperature of the molten metal to 615°C and pour it into a stainless steel mold. The inner diameter of the mold is 50mm, and the height is 100mm. Continue to reduce the temperature of the metal slurry, and control the temperature at 595±5°C to prepare the Al-7Si-0.4Mg-0.1Er alloy semi-solid slurry. At this time, the alloy is in the semi-solid range. Take the semi-solid alloy out...
Embodiment 2
[0021] Embodiment 2: First, 581.7 g of high-purity aluminum (purity is 99.99%) and 838.4 g of Al-12% Si master alloy are added in a graphite clay crucible, and the alloy is melted in a resistance furnace at a melting temperature of 750° C. After the metal is completely melted, press 6.4g of pure Mg (99.9% purity) into the metal melt with a bell jar, and the alloy is heated at 720°C with C 2 Cl 6 Degassing and refining. After standing still for 20 minutes, the temperature was raised to 750°C and 75g of Al-6% Er master alloy was added. A K-type thermocouple is used to monitor the temperature of the molten metal. Lower the temperature of the molten metal to 615°C and pour it into a stainless steel mold with an inner diameter of 50mm and a height of 100mm. Continue to reduce the temperature of the metal slurry, and control the temperature at 595±5°C to prepare an Al-7Si-0.4Mg-0.3Er alloy semi-solid slurry. At this time, the alloy is in the semi-solid range, and the semi-solid a...
Embodiment 3
[0022] Embodiment 3: First, 531.7 g of high-purity aluminum (purity is 99.99%) and 838.4 g of Al-12% Si master alloy are added in a graphite clay crucible, and the alloy is melted in a resistance furnace at a melting temperature of 750° C. After the metal is completely melted, press 6.4g of pure Mg (99.9% purity) into the metal melt with a bell jar, and the alloy is heated at 720°C with C 2 Cl 6 Degassing and refining. After standing still for 20 minutes, raise the temperature to 750°C and add 125g Al-6% Er master alloy. A K-type thermocouple is used to monitor the temperature of the molten metal. Lower the temperature of the molten metal to 630°C and pour it into a stainless steel mold with an inner diameter of 50mm and a height of 100mm. Continue to reduce the temperature of the metal slurry, and control the temperature at 595±5°C to prepare an Al-7Si-0.4Mg-0.5Er alloy semi-solid slurry. At this time, the alloy is in the semi-solid range, and the semi-solid alloy is taken...
PUM
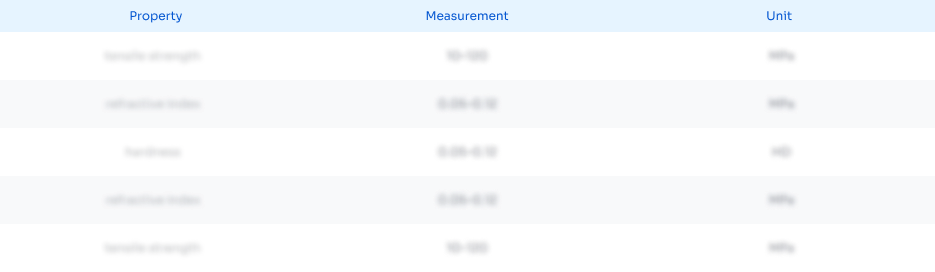
Abstract
Description
Claims
Application Information

- Generate Ideas
- Intellectual Property
- Life Sciences
- Materials
- Tech Scout
- Unparalleled Data Quality
- Higher Quality Content
- 60% Fewer Hallucinations
Browse by: Latest US Patents, China's latest patents, Technical Efficacy Thesaurus, Application Domain, Technology Topic, Popular Technical Reports.
© 2025 PatSnap. All rights reserved.Legal|Privacy policy|Modern Slavery Act Transparency Statement|Sitemap|About US| Contact US: help@patsnap.com