One-step leaven washing method
A step-by-step enzyme and enzyme technology, which is applied in the field of denim reconditioning and washing process, can solve the problems of difficulty in popularization and application and long process, and achieve excellent anti-restaining performance, simplify the washing process, and shorten the washing time.
- Summary
- Abstract
- Description
- Claims
- Application Information
AI Technical Summary
Problems solved by technology
Method used
Examples
Embodiment 1
[0023] Add water to 1 kg of jeans at a bath ratio of 1:12, add 1.4% (o.w.f) washing enzyme, heat up to 50°C, wash at a constant temperature for 45 minutes, drain, add water, calculate the total volume, add additives at 0.01-0.02g / l, and wash 10min, take the clothes and spin dry, dry; the washing enzyme used is produced by Nanjing Chuanping Science and Technology Development Co., Ltd.; the washing method used can be enzyme water washing or enzyme stone mill washing, and the pH of the water used is 7.2, without adding acetic acid to adjust, so The auxiliary agent described is sodium carbonate. After the water washing, compared with the denim clothes washed with the current two-step process, there is no difference in the aspects of returning to the old, blooming, anti-re-staining and hair removal, and there are no streaks. The finishing quality of denim is good, and a good cost saving effect has been achieved, see the table below for details
[0024] Comparison of production cos...
Embodiment 2
[0031] Add 1.8% (o.w.f) washing enzyme to 1 kg of jeans at a bath ratio of 1:17, raise the temperature to 50°C, wash at a constant temperature for 40 minutes, drain, add water, and add additives at 0.01-0.02 g / l to calculate the total volume, and wash for 10 minutes , take the clothes, spin dry, and dry; the washing enzyme used is produced by Nanjing Chuanping Technology Development Co., Ltd. The washing method used can be enzyme water washing or enzyme stone mill washing. The pH of the water used is 6.8-7.0, without adding acetic acid to adjust, Described auxiliary agent is sodium carbonate. After washing in water, compared with the jeans washed with water by the current two-step process, there is no difference in the aspects of aging, flowering, anti-restaining and hair removal. There are no spots and stripes, and the denim The finishing quality of the cloth is good, and good economic results have been achieved, see the table below for details
[0032] Comparison of product...
Embodiment 3
[0038] Add water to 1 kg of jeans at a bath ratio of 1:20, add 2.6% (o.w.f) washing enzyme, heat up to 50°C, wash at a constant temperature for 40 minutes, drain, add water, calculate the total volume, add additives at 0.01-0.02g / l, and wash 10 minutes, take out the clothes, spin dry, and dry; the washing enzyme used is produced by Nanjing Chuanping Technology Development Co., Ltd. The washing method used can be enzyme water washing or enzyme stone mill washing. The pH of the water used is 6.5-7.0, without adding acetic acid to adjust , the auxiliary agent is sodium carbonate. After washing in water, compared with the jeans washed with water by the current two-step process, there are no spots and streaks, and the finishing quality of the denim is good, which has achieved good results. Economic effects, see the table below
[0039] Comparison of production costs between traditional process and one-step process
[0040]
craft
processing time
/ min ...
PUM
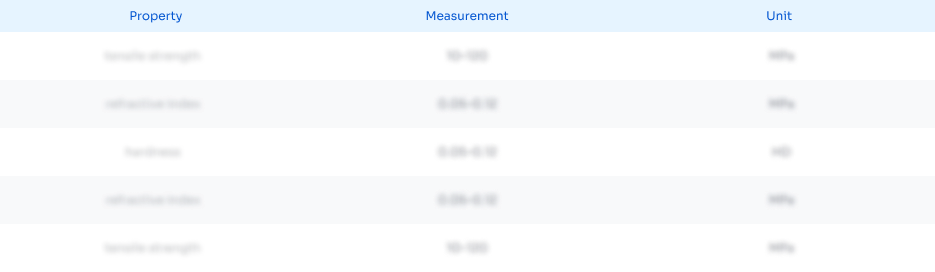
Abstract
Description
Claims
Application Information

- R&D
- Intellectual Property
- Life Sciences
- Materials
- Tech Scout
- Unparalleled Data Quality
- Higher Quality Content
- 60% Fewer Hallucinations
Browse by: Latest US Patents, China's latest patents, Technical Efficacy Thesaurus, Application Domain, Technology Topic, Popular Technical Reports.
© 2025 PatSnap. All rights reserved.Legal|Privacy policy|Modern Slavery Act Transparency Statement|Sitemap|About US| Contact US: help@patsnap.com