Sliding formwork control method used in motion control of virtual axis machine tool cutter
A virtual axis machine tool and motion control technology, applied in the field of virtual axis machine tools, can solve problems affecting the accuracy of the sliding mode control method, achieve the effects of reducing debugging workload, solving tremor problems, and excellent control quality
- Summary
- Abstract
- Description
- Claims
- Application Information
AI Technical Summary
Problems solved by technology
Method used
Image
Examples
Embodiment
[0059] Assuming that the virtual axis machine tool is composed of 6 branch parallel mechanisms, driven by AC servo motors, and adopts rolling screw transmission (ball screw), the block diagram of its control system is as follows figure 1 shown. The specific implementation of this control method is as follows:
[0060] 1. Determine the expected movement of each active pair of the virtual axis machine tool according to the processing requirements in advance
[0061] Assume that according to the processing requirements, the tool needs to move linearly from the (20mm, 20mm, 20mm) space point to the (30mm, 30mm, 30mm) space point. According to the inverse solution of the kinematics of the virtual axis machine tool, the expected motion trajectories of the active pairs of each branch of the virtual axis machine tool are obtained as follows: figure 2 The traces of the small circles in each subfigure are shown.
[0062] 2. Pre-establish the transfer function of each branch control ...
PUM
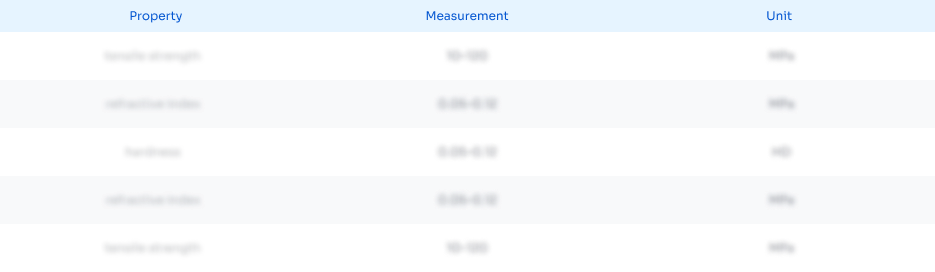
Abstract
Description
Claims
Application Information

- R&D Engineer
- R&D Manager
- IP Professional
- Industry Leading Data Capabilities
- Powerful AI technology
- Patent DNA Extraction
Browse by: Latest US Patents, China's latest patents, Technical Efficacy Thesaurus, Application Domain, Technology Topic, Popular Technical Reports.
© 2024 PatSnap. All rights reserved.Legal|Privacy policy|Modern Slavery Act Transparency Statement|Sitemap|About US| Contact US: help@patsnap.com