Measuring method of tunnel shield posture
A measurement method and technology for tunnel shielding, which are applied in tunnels, earth-moving drilling, mining equipment, etc., can solve the problems that affect the progress of the project, the automatic measurement system is prone to problems, and is difficult to repair, so as to save project costs and ensure measurement accuracy. and stability, the effect of simplifying the measurement process
- Summary
- Abstract
- Description
- Claims
- Application Information
AI Technical Summary
Problems solved by technology
Method used
Image
Examples
Embodiment Construction
[0056] Attached below Figure 1-9 A preferred embodiment of the method of the present invention will be described in detail.
[0057] like figure 1 , 9As shown, a front instrument platform 1 and a rear instrument platform 2 are arranged on the segment 8 assembled at the rear of the shield machine 7 one in front of the other at a distance of 30 to 35 cm from the top of the segment 8, and the interval at the lower part of the front instrument platform 1 is 40 cm. The front instrument console 9 is arranged on the left and right, the theodolite 4 is arranged at intervals on the front instrument platform 1; the rear instrument console 10 is arranged at an interval of about 40 cm at the bottom of the rear instrument platform 2, and the prism 3 is arranged on the rear instrument platform 2, the structural representation of the prism 3 like Figure 5 shown. Surveyors stand on the instrument consoles 9 and 10 and operate the theodolite 4 or prism 3 for measurement. like image 3 ...
PUM
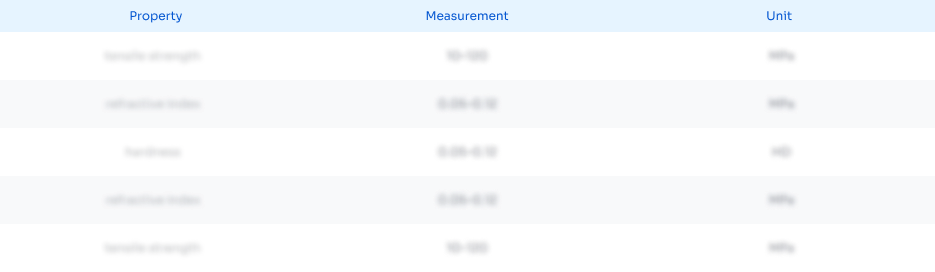
Abstract
Description
Claims
Application Information

- R&D
- Intellectual Property
- Life Sciences
- Materials
- Tech Scout
- Unparalleled Data Quality
- Higher Quality Content
- 60% Fewer Hallucinations
Browse by: Latest US Patents, China's latest patents, Technical Efficacy Thesaurus, Application Domain, Technology Topic, Popular Technical Reports.
© 2025 PatSnap. All rights reserved.Legal|Privacy policy|Modern Slavery Act Transparency Statement|Sitemap|About US| Contact US: help@patsnap.com