Head lamellae pressing-molding die
A technology of press molding and head flaps, which is applied in the direction of forming tools, manufacturing tools, assembly machines, etc., to achieve the effects of low replacement cost, high overall rigidity and long service life
- Summary
- Abstract
- Description
- Claims
- Application Information
AI Technical Summary
Problems solved by technology
Method used
Image
Examples
Embodiment 1
[0020] A head flap pressing mold of this embodiment, the overall structure of the mold is shown in the attached figure 1 , template and locating piece locating key 6, initial locating block 9 are made of 45# steel plate; the mold body is a casting, and its material should meet the requirements of 45# steel; insert heat-resistant steel insert 4 is 5CrNiMo refined heat-resistant steel forging ; Connectors are standard.
[0021] The processing process is: determine the main size of the mold→detail design of the mold→mold manufacturing→press test→calculate the springback angle of the workpiece and the compensation amount of the mold→repair the mold→press test→calculate the springback angle of the workpiece and the compensation amount of the mold→repair the mold until The radius of the obtained workpiece meets the design requirements.
[0022] The mold adopts building block assembly structure, as attached figure 2 shown. Each set of mold consists of upper template 1, lower temp...
PUM
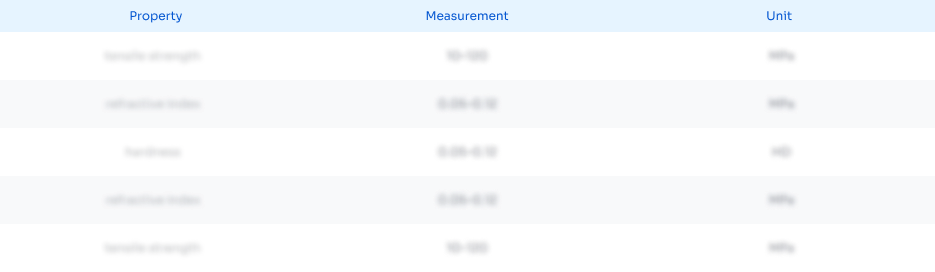
Abstract
Description
Claims
Application Information

- Generate Ideas
- Intellectual Property
- Life Sciences
- Materials
- Tech Scout
- Unparalleled Data Quality
- Higher Quality Content
- 60% Fewer Hallucinations
Browse by: Latest US Patents, China's latest patents, Technical Efficacy Thesaurus, Application Domain, Technology Topic, Popular Technical Reports.
© 2025 PatSnap. All rights reserved.Legal|Privacy policy|Modern Slavery Act Transparency Statement|Sitemap|About US| Contact US: help@patsnap.com