Cold sling method and device
A catapult device and catapult technology, applied in the direction of launching/dragging transmissions, etc., can solve the problems of high and unstable speed, difficult coupling of energy storage and load, missing fighters, etc., so as to achieve less operation and maintenance personnel and reduce ejection power consumption , the effect of large degree of freedom of energy collection
- Summary
- Abstract
- Description
- Claims
- Application Information
AI Technical Summary
Problems solved by technology
Method used
Image
Examples
specific Embodiment approach
[0040] see figure 1 , figure 2 , this embodiment 1 adopts a three-stage gas-liquid fusion oil cylinder 1, a two-position three-way electromagnetic control valve 1-1, a high-energy gas source 5, a gas cylinder 6, an energy recovery pump 2-4, a jump cylinder 2-2 and a limit Buffer springs are arranged in the oil retaining cylinders 3, and damping holes 3-1 are provided in the limit oil retaining cylinders 3. Usually, according to the ejection conditions given by the superior, the digitally controlled high-energy gas source 5 collects and stores the required high-energy gas in the gas cylinder 6, and then shuts down and stands by. In its cold state with its mechanics fully closed, the catapult remains ready to fire at all times. In wartime, under the cold condition of its mechanical complete shutdown, without preparation time, the two-position three-way electromagnetic control valve 1-1 can be energized to control part of the high-energy gas in the gas cylinder 6 to enter the ...
PUM
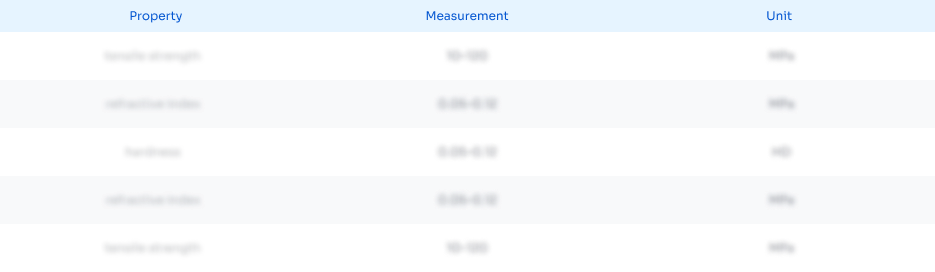
Abstract
Description
Claims
Application Information

- Generate Ideas
- Intellectual Property
- Life Sciences
- Materials
- Tech Scout
- Unparalleled Data Quality
- Higher Quality Content
- 60% Fewer Hallucinations
Browse by: Latest US Patents, China's latest patents, Technical Efficacy Thesaurus, Application Domain, Technology Topic, Popular Technical Reports.
© 2025 PatSnap. All rights reserved.Legal|Privacy policy|Modern Slavery Act Transparency Statement|Sitemap|About US| Contact US: help@patsnap.com