Preparation method of polyvinyl chloride resin containing brucite and capable of being processed directly
The technology of polyvinyl chloride resin and hydrotalcite is applied in the field of preparation of directly processable polyvinyl chloride resin, which can solve the problems of reducing the density of burning smoke and the like, and achieve the effect of good thermal stability.
- Summary
- Abstract
- Description
- Claims
- Application Information
AI Technical Summary
Problems solved by technology
Method used
Examples
Embodiment 1
[0020] Adopt wet method, with stearic acid surface modification magnesium / aluminum ratio is 2 / 1, interlayer anion is the hydrotalcite of carbonate group (Dalian Fumeida New Material Co., Ltd); the hydrotalcite of 0.5g surface modification, 2.5 Add g Ca / Zn composite heat stabilizer, 0.10g diethylhexyl peroxydicarbonate, 100g vinyl chloride, 0.15g polyvinyl alcohol dispersant and 200g deionized water into the reactor, stir, and heat up to 57°C for polymerization Reaction, when the pressure of the polymerization system drops by 2.0kg / cm 2When the reaction is finished, unreacted vinyl chloride is reclaimed, discharged, filtered, and dried to obtain 86.5g of hydrotalcite-containing PVC resin that can be directly processed. The heat stability time of the processed PVC pellets at 180° C. is 75 minutes.
Embodiment 2
[0022] Using a wet method, the hydrotalcite (Dalian Fumeida New Material Co., Ltd.) with stearic acid surface modified magnesium / aluminum ratio of 2 / 1 and interlayer anion as carbonate; 0.1g modified hydrotalcite, 3.0g Ca / Zn composite heat stabilizer, 0.10g diethylhexyl peroxydicarbonate, 100g vinyl chloride, 0.15g polyvinyl alcohol dispersant and 200g deionized water are added to the reactor, stirred, and the temperature is raised to 57° C. to start the polymerization reaction. The pressure drop of the polymerization system is 2.0kg / cm 2 When the reaction is finished, unreacted vinyl chloride is recovered, discharged, filtered, and dried to obtain 87.0 g of hydrotalcite-containing PVC resin that can be directly processed. The thermal stability time of the processed PVC pellets at 180° C. was 82 minutes.
Embodiment 3
[0024] Adopt wet method, with stearic acid surface modification magnesium / aluminum ratio is 2 / 1, interlayer anion is the hydrotalcite of carbonate (Dalian Fumeida New Material Co., Ltd.); 1.0g modified hydrotalcite, 2.5g Ca / Zn composite heat stabilizer, 0.10g diethylhexyl peroxydicarbonate, 100g vinyl chloride, 0.15g polyvinyl alcohol dispersant and 200g deionized water were added to the reactor, stirred, and the temperature was raised to 57°C to start the polymerization reaction. When the pressure of the polymerization system drops by 2.0kg / cm 2 When the reaction was finished, the unreacted vinyl chloride was recovered, discharged, filtered, and dried to obtain 86.5g of directly processable polyvinyl chloride resin containing hydrotalcite. The thermal stability time of the processed PVC pellets at 180° C. was 72 minutes.
PUM
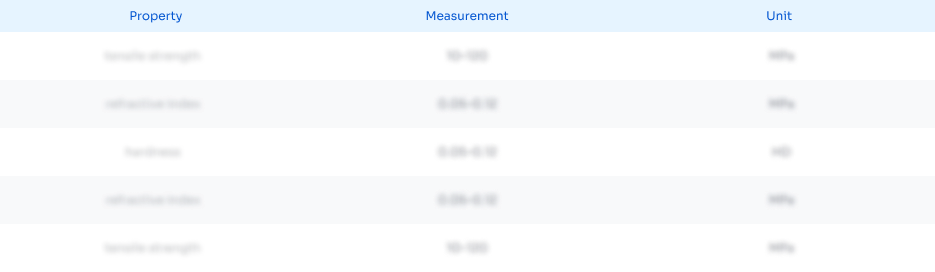
Abstract
Description
Claims
Application Information

- R&D
- Intellectual Property
- Life Sciences
- Materials
- Tech Scout
- Unparalleled Data Quality
- Higher Quality Content
- 60% Fewer Hallucinations
Browse by: Latest US Patents, China's latest patents, Technical Efficacy Thesaurus, Application Domain, Technology Topic, Popular Technical Reports.
© 2025 PatSnap. All rights reserved.Legal|Privacy policy|Modern Slavery Act Transparency Statement|Sitemap|About US| Contact US: help@patsnap.com