Preparation method of fine graphite
A fine structure, graphite technology, applied in the field of fine structure graphite preparation, can solve the problems of easy formation of cracks, low qualified rate of finished products, etc., to solve the crack problem, shorten the production cycle, and solve the effect of product cracks.
- Summary
- Abstract
- Description
- Claims
- Application Information
AI Technical Summary
Problems solved by technology
Method used
Examples
Embodiment 1
[0021] The preparation method of fine structure graphite, coke fine powder and asphalt fine powder are fully mixed with the mass ratio dry method of 10:1, and the mixture is in the airtight mold that vacuum degree is 0.005Mpa, temperature is 350 ℃ (mold is cylindrical , diameter 600mm, height 600mm) heating for 7h, while adding vibration until the density of the mixture is not less than 1.8g / cm 3 ; After that, apply 50t pressure to the mold and gradually raise the temperature to 900°C to sinter to obtain fine-structure graphite. The entire heating and sintering process lasts for 18 hours, and is heated and roasted in a resistance furnace.
Embodiment 2
[0023] The preparation method of fine structure graphite, coke fine powder and asphalt fine powder are fully mixed with the mass ratio dry method of 4: 1, and the mixture is in the airtight mold that vacuum degree is 0.009Mpa, temperature is 250 ℃ (mold is cylindrical , diameter 300mm, height 600mm) heating for 5 hours, while adding vibration until the density of the mixture is not less than 1.8g / cm 3 ; Then apply 30t pressure to the mold and gradually raise the temperature to 1200°C to sinter to obtain fine-structure graphite. The entire heating and sintering process lasts for 10 hours, and is heated and roasted in a resistance furnace.
Embodiment 3
[0025] The preparation method of fine structure graphite, coke fine powder and asphalt fine powder are fully mixed with the mass ratio dry method of 7: 3, and the mixture is in the airtight mold that vacuum degree is 0.008Mpa, temperature is 300 ℃ (mold is cylindrical , diameter 700mm, height 600mm) heating for 8 hours, while adding vibration until the density of the mixture is not less than 1.8g / cm 3 ; After that, apply 40t pressure to the mold and gradually raise the temperature to 1000°C to sinter to obtain fine-structure graphite. The whole heating and sintering process lasts for 20 hours, and is heated and roasted in a resistance furnace.
PUM
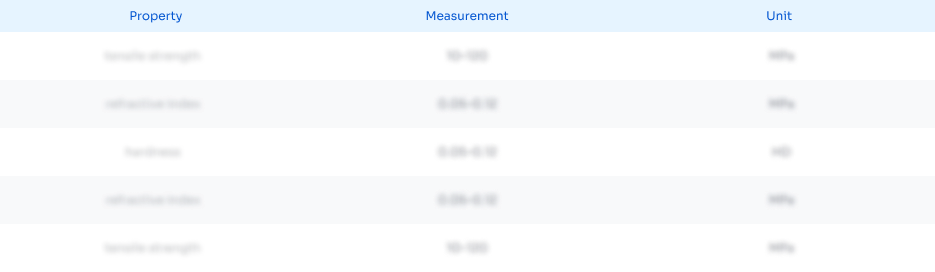
Abstract
Description
Claims
Application Information

- R&D
- Intellectual Property
- Life Sciences
- Materials
- Tech Scout
- Unparalleled Data Quality
- Higher Quality Content
- 60% Fewer Hallucinations
Browse by: Latest US Patents, China's latest patents, Technical Efficacy Thesaurus, Application Domain, Technology Topic, Popular Technical Reports.
© 2025 PatSnap. All rights reserved.Legal|Privacy policy|Modern Slavery Act Transparency Statement|Sitemap|About US| Contact US: help@patsnap.com