Engagement chain type driving device
A driving device and meshing technology, which is applied to portable lifting devices, hoisting devices, hoisting devices, etc., can solve the problems of damage to the design freedom of the device, reduced bending strength, and complexity, so as to ensure rigidity, stable forward and backward drive, and improve bending intensity effect
- Summary
- Abstract
- Description
- Claims
- Application Information
AI Technical Summary
Problems solved by technology
Method used
Image
Examples
Embodiment Construction
[0034] The meshing chain type lifting device of the present invention can be implemented in any way as long as it is the following device. Opposite each other in the same plane, and rotate forward and reverse in opposite directions; a pair of meshing chains, on the one hand, are integrated through a pair of driving sprockets, and on the other hand, are mutually meshed and disengaged through a pair of driving sprockets And separate; and the drive source, which drives a pair of drive sprockets, respectively forming a curved limiting flat surface to maintain the meshing posture of the chain on the inner tooth piece and the outer tooth piece constituting the meshing chain, and meshing into one by using the driving sprocket In the state where the inner tooth pieces and the outer tooth pieces face each other, the above-mentioned bending restricting flat surfaces come into surface contact with each other, thereby realizing stable forward and backward driving of the workpiece without p...
PUM
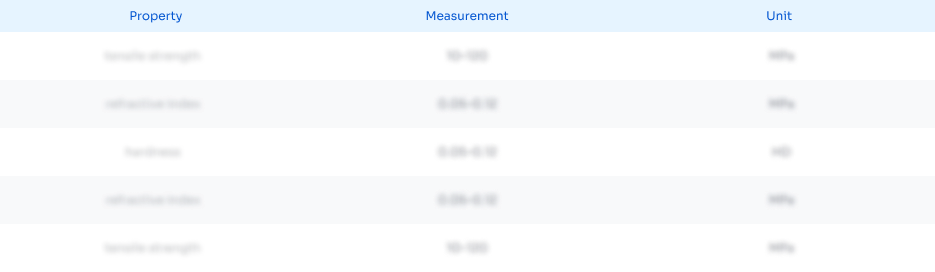
Abstract
Description
Claims
Application Information

- R&D
- Intellectual Property
- Life Sciences
- Materials
- Tech Scout
- Unparalleled Data Quality
- Higher Quality Content
- 60% Fewer Hallucinations
Browse by: Latest US Patents, China's latest patents, Technical Efficacy Thesaurus, Application Domain, Technology Topic, Popular Technical Reports.
© 2025 PatSnap. All rights reserved.Legal|Privacy policy|Modern Slavery Act Transparency Statement|Sitemap|About US| Contact US: help@patsnap.com