Preparation method of nanometer zirconia heat barrier coating
A nano-zirconia and thermal barrier coating technology, applied in coating, metal material coating process, air transportation, etc., can solve the problems of complex thermal barrier coating equipment and high preparation cost, and achieve low cost and good fluidity. , The effect of good sol dispersion
- Summary
- Abstract
- Description
- Claims
- Application Information
AI Technical Summary
Problems solved by technology
Method used
Image
Examples
Embodiment 1
[0040] Embodiment 1: take by weighing 730 grams of crystal ZrOCl 2 ·8H 2 O (molar mass 322.22g / mol, i.e. about 2.27mol in 730g) is dissolved in the mixed solvent (1:1) of absolute ethanol and deionized water; in order to make the zirconium ion concentration in the solution be 1.5mol / L, the mixed solvent The volume is about 1.51L (i.e. 751ml each of dehydrated ethanol and deionized water), and then doped with crystalline rare earth oxides to control yttrium oxide to account for 7% of the total mass of raw materials (mass fraction, i.e. add 70 grams), cerium oxide and The mass fraction of lanthanum oxide is 10% (mass fraction, that is, add 100 grams each). Add polymer active dispersant-polyethylene glycol PEG20000 and PEG1750 ± 50 each 0.5% (mass fraction, promptly add 5 grams each) in the solution, water bath control temperature is 80 ℃, and keep stirring, then add pH= 9-10 ammonia water, adjust the pH value of the solution with ammonia water positive titration until the pH o...
Embodiment 2
[0042] Embodiment 2: prepare and purify hydroxide sol by the method for embodiment 1. Adjust the feeding rate of the hydroxide sol to 120g / min, and atomize it into droplets of a certain size under the air pressure of 0.5MPa, keep other plasma spraying parameters unchanged, and send the atomized droplets into the plasma flame , and deposited on the substrate to obtain a zirconia coating. Measure the thermal conductivity of the coating that this embodiment prepares with laser scintillation method, measurement result is as table 3; Measure the thermal shock cycle number of this coating with the method for forced air cooling, the result is as table 4; Measure coating with X-ray diffraction The crystal structure, the results are shown in Table 2.
Embodiment 3
[0043] Embodiment 3: adjust the zirconium ion concentration in the solution to 0.8mol / L, prepare and purify hydroxide sol by the method for embodiment 1; Adjust the feed rate of hydroxide sol to 150g / min, and under air pressure It is atomized into droplets of a certain size under 0.5MPa, keeping other plasma spraying parameters unchanged, sending the atomized droplets into the plasma flame, and depositing them on the substrate to obtain a zirconia coating. Measure the thermal conductivity of the coating that this embodiment prepares with laser scintillation method, measurement result is as table 3; Measure the thermal shock cycle number of this coating with the method for forced air cooling, the result is as table 4; Measure coating with X-ray diffraction The results showed that the coating still contained 5% monoclinic zirconia.
PUM
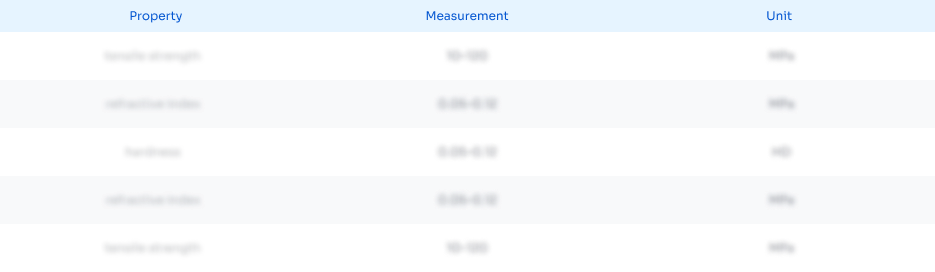
Abstract
Description
Claims
Application Information

- R&D
- Intellectual Property
- Life Sciences
- Materials
- Tech Scout
- Unparalleled Data Quality
- Higher Quality Content
- 60% Fewer Hallucinations
Browse by: Latest US Patents, China's latest patents, Technical Efficacy Thesaurus, Application Domain, Technology Topic, Popular Technical Reports.
© 2025 PatSnap. All rights reserved.Legal|Privacy policy|Modern Slavery Act Transparency Statement|Sitemap|About US| Contact US: help@patsnap.com