Ceramic glaze pattern-glazed brick and production method thereof
A production method and technology for polishing glazed tiles, applied in the field of ceramic products, can solve the problems of the influence of color varieties, microcrystalline stone is not wear-resistant, and the color varieties are monotonous, etc., and achieves strong transparency, good wear resistance, and reduced glaze porosity. Effect
- Summary
- Abstract
- Description
- Claims
- Application Information
AI Technical Summary
Problems solved by technology
Method used
Image
Examples
Embodiment Construction
[0027] The present invention will be further described below in conjunction with specific examples, but not as a limitation to the present invention.
[0028] A kind of production method of glazed tile in porcelain glaze, comprising the following steps:
[0029] 1. Combined green body formula;
[0030] 1.1. The approximate chemical composition of the green body is calculated by weight percentage: SiO 2 : 69-72%, Al 2 o 3 : 18-20%, k 2 O+Na 2 O: 6-7.5%, CaO+MgO≤2.9%, Fe 2 o 3 +TiO 2 <1%, loss on ignition should be <4%, and the volatilization distribution in the material is: 26-33% of clay, 25-30% of sand, 35-40% of stone powder, and 2-3% of talc.
[0031] The selected green body formula: black mud 15% white mud 12%, high temperature sand 10%, medium temperature sand 11%, low temperature sand 16%, potassium stone powder 17% sodium stone powder 16%, raw talc 3%, with a size of 600×600mm as Example is 7.6kg.
[0032] 1.2. The process parameter control of slurry and powde...
PUM
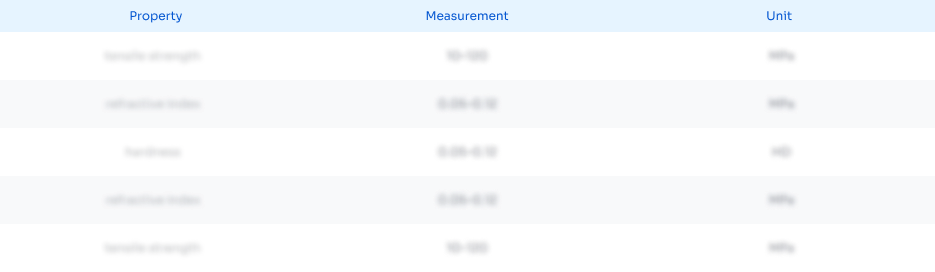
Abstract
Description
Claims
Application Information

- R&D
- Intellectual Property
- Life Sciences
- Materials
- Tech Scout
- Unparalleled Data Quality
- Higher Quality Content
- 60% Fewer Hallucinations
Browse by: Latest US Patents, China's latest patents, Technical Efficacy Thesaurus, Application Domain, Technology Topic, Popular Technical Reports.
© 2025 PatSnap. All rights reserved.Legal|Privacy policy|Modern Slavery Act Transparency Statement|Sitemap|About US| Contact US: help@patsnap.com