Reverse reaming countersink inner end face knife
An inner face, reaming technology, applied in the direction of reamer, reaming device, drilling/drilling equipment, etc., can solve problems such as difficulty, runout tolerance, etc., to reduce processes, improve processing efficiency, and ensure processing size and position. The effect of tolerance
- Summary
- Abstract
- Description
- Claims
- Application Information
AI Technical Summary
Problems solved by technology
Method used
Image
Examples
Embodiment Construction
[0013] The accompanying drawing is the reverse reaming countersink inner end face cutter used for processing the cylinder head of 16V240 diesel engine on the vertical power head. In the accompanying drawings, the tool taper shank on the tool bar is installed in the taper hole of the power head main shaft (1), the external thread of the fixed sleeve (2) on the tool bar is installed in the screw hole of the main shaft (1), and the fixed sleeve ( 2) The inner end face of the tool is pressed on the shoulder of the cylinder below the tool taper handle; the reamed spot facing inner end face knife is installed on the cone at the lower end of the tool bar through its taper hole and connected by a key (12), and is connected with a locking handle ( 8) Fixed, the reaming countersinking inner end face knife has a positioning structure to control the depth of the reaming hole countersinking inner end face; there is a small hole (conduit hole) processed with the part (13) (cylinder head) on ...
PUM
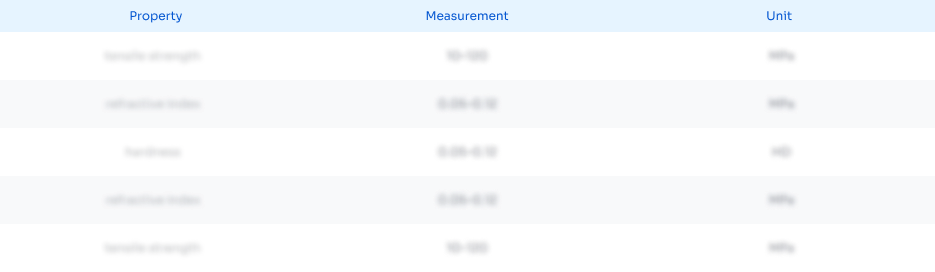
Abstract
Description
Claims
Application Information

- R&D
- Intellectual Property
- Life Sciences
- Materials
- Tech Scout
- Unparalleled Data Quality
- Higher Quality Content
- 60% Fewer Hallucinations
Browse by: Latest US Patents, China's latest patents, Technical Efficacy Thesaurus, Application Domain, Technology Topic, Popular Technical Reports.
© 2025 PatSnap. All rights reserved.Legal|Privacy policy|Modern Slavery Act Transparency Statement|Sitemap|About US| Contact US: help@patsnap.com