Method for preparing catalyst used in selective oxo-synthesis of crylic acid from propane
A technology for selective oxidation and acrylic acid, applied in metal/metal oxide/metal hydroxide catalysts, physical/chemical process catalysts, chemical instruments and methods, etc., can solve the problem of low propane reactivity and achieve high acrylic acid selectivity and yield effects
- Summary
- Abstract
- Description
- Claims
- Application Information
AI Technical Summary
Problems solved by technology
Method used
Image
Examples
Embodiment 1
[0023] The Mo-V-Te-Nb-O catalyst was prepared by the in-situ hydrothermal synthesis method, and the stoichiometric ammonium molybdate, vanadyl sulfate, telluric acid and niobium oxalate were respectively dissolved in hot deionized water, heated and stirred for 30min~ After 60 minutes, slowly mix the solutions together one by one, continue to stir for 30 minutes to 60 minutes, then pour all the mixed solutions into the reaction kettle, and put them in an oven for in-situ aging. The aging temperature is 170-230°C and the aging time is 40 minutes. ~70 hours. Then, it is taken out, filtered, dried, calcined at 500-700° C. for 2-5 hours, and crushed into 20-60 meshes. The catalyst sample prepared by this in-situ hydrothermal synthesis method was carried out by XRD powder diffraction method, and the results were as follows: figure 1 As shown, the electron microscope photos are as figure 2 shown.
Embodiment 2
[0025] The Mo-V-Te-Nb-O catalyst prepared in Example 1 was used in the reaction of propane to acrylic acid. Weigh about 2g of 20-60 mesh catalyst, and the reaction raw material gas ratio V(C 3 h 8 ): V(air): V(vapor)=1:15:12, the reaction pressure is normal pressure, the reaction temperature is 380°C, and the reaction space velocity is 800L Kg -1 h -1 , the reaction time is 2 hours. The conversion of propane was 63.7%, the selectivity of acrylic acid was 73.6%, and the yield was 46.9%.
Embodiment 3
[0027] Different batches of Mo-V-Te-Nb-O catalysts prepared in Example 1 were used in the reaction of propane to acrylic acid. Weigh about 2g of 20-60 mesh catalyst, and the reaction raw material gas ratio V(C 3 h 8 ): V(air): V(vapor)=1:15:12, the reaction pressure is normal pressure, the reaction temperature is 400°C, and the reaction space velocity is 800L Kg -1 h -1 , the reaction time is 2 hours. The result of the reaction is as image 3 As shown, the yield of acrylic acid is not much different, and the results of the two repetitions are very similar. It is proved that the catalyst prepared by the in situ hydrothermal synthesis method has very good repeatability of catalytic activity.
PUM
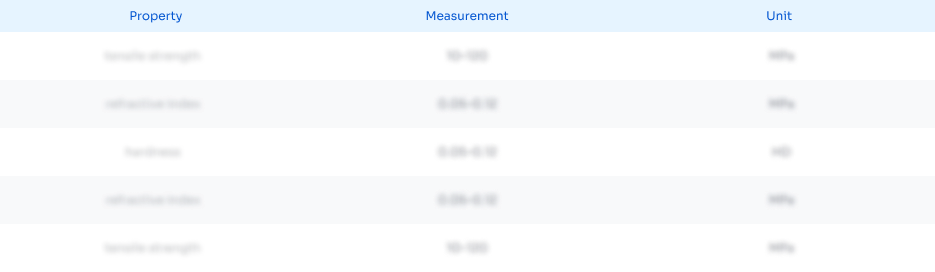
Abstract
Description
Claims
Application Information

- Generate Ideas
- Intellectual Property
- Life Sciences
- Materials
- Tech Scout
- Unparalleled Data Quality
- Higher Quality Content
- 60% Fewer Hallucinations
Browse by: Latest US Patents, China's latest patents, Technical Efficacy Thesaurus, Application Domain, Technology Topic, Popular Technical Reports.
© 2025 PatSnap. All rights reserved.Legal|Privacy policy|Modern Slavery Act Transparency Statement|Sitemap|About US| Contact US: help@patsnap.com