Projection bolt welding method, and welding apparatus
A welding device and welding method technology, applied in the direction of welding/welding/cutting items, auxiliary devices, welding equipment, etc., can solve the problems of difficulty in manufacturing, wear of movable parts, and installation space constraints, and achieve a quiet and compact factory environment. effect of size
- Summary
- Abstract
- Description
- Claims
- Application Information
AI Technical Summary
Problems solved by technology
Method used
Image
Examples
Embodiment 1
[0118] Figure 1~ Figure 7 Example 1 is shown.
[0119] Describes projection welding bolts.
[0120] Such as Figure 2B As shown, the projection welding bolt 10 is made of iron, a circular flange portion 12 is integrally formed on the shaft portion 11 , and a circular welding protrusion 13 is provided on the flange surface opposite to the shaft portion 11 . Furthermore, the flange portion 12 is in a state concentric with the shaft portion 11 . The dimensions of each part are as follows, the diameter of the shaft portion 11 is 5 mm, the length of the shaft portion 11 is 23 mm, the diameter of the flange portion is 13 mm, the thickness of the flange portion is 1 mm, the diameter of the welding protrusion 13 is 9 mm, and the welding protrusion 13 The protrusion thickness is 1.2mm. In addition, in the following description, a projection welding bolt may be simply described as a bolt.
[0121] The overall welding device will be described.
[0122] Figure 1A It is a side view...
Embodiment 2
[0210] Figure 8 Example 2 is shown.
[0211] In this second embodiment, the resistance welding device 100 in the above-mentioned first embodiment is changed to a C-type welding torch. Accordingly, an engaging member 69 is fixed to the C-shaped arm 68 , and the piston rod 22 of the air cylinder 21 is fixed to the engaging member 69 . Furthermore, the above-mentioned base member 14 is connected to the cylinder 21 . In addition, another automatic device 70 is connected to the joint member 69 . Other configurations include unillustrated parts and are the same as those of the first embodiment, and the same symbols are assigned to components with the same functions. In addition, the operation and effect are also the same as those of the first embodiment described above.
Embodiment 3
[0213] Figure 9 Example 3 is shown.
[0214] In the previous embodiments, the supply rod 17 advances and retreats obliquely with respect to the electrode axis ○-○. In this third embodiment, the supply rod 17 advances and retreats in a direction perpendicular to the electrode axis ○-○. And after the supply rod 17 is raised by the air cylinder 21 and inserts the front end portion of the shaft portion 11 into the receiving hole 20, the insertion of the bolt 10 is completed by air jet. As a result, after the insertion is completed, the supply rod 17 is retracted without descending. That is, a rectangular movement indicated by symbol 71 is performed.
[0215] Therefore, in the third embodiment, after the bolt 10 is inserted into the receiving hole 20 by the air jet, the supply rod 17 is retracted from the original position by the air cylinder 16 . In the case of performing such an operation, the lowering operation of the supply rod 17 can be terminated in accordance with a retr...
PUM
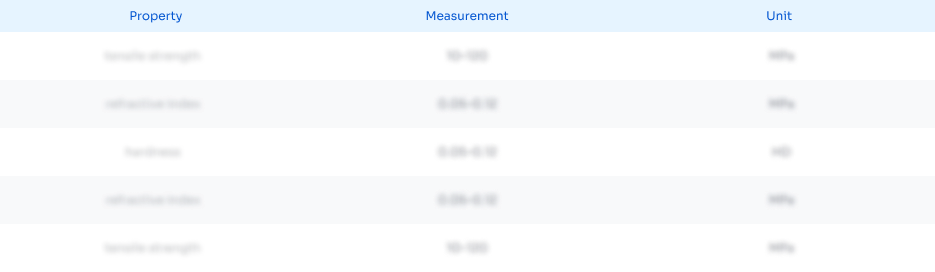
Abstract
Description
Claims
Application Information

- R&D
- Intellectual Property
- Life Sciences
- Materials
- Tech Scout
- Unparalleled Data Quality
- Higher Quality Content
- 60% Fewer Hallucinations
Browse by: Latest US Patents, China's latest patents, Technical Efficacy Thesaurus, Application Domain, Technology Topic, Popular Technical Reports.
© 2025 PatSnap. All rights reserved.Legal|Privacy policy|Modern Slavery Act Transparency Statement|Sitemap|About US| Contact US: help@patsnap.com