Method for manufacturing automobile glass wool insulating mat
A production method, the technology of automotive glass, applied in the field of automotive interior parts, can solve the problems of heavy product weight, poor product rigidity, easy to break, etc., and achieve the effect of low purchase cost, reduced weight, and not easy to break
- Summary
- Abstract
- Description
- Claims
- Application Information
AI Technical Summary
Problems solved by technology
Method used
Examples
Embodiment 1
[0015] Example 1: The production process steps of GAC Toyota Highlander machine cover heat insulation pad are as follows:
[0016] 1. Paving. The laying steps are as follows: (1). First lay the base fabric as impregnated non-woven fabric (PE film upward), (2). Cut glass wool (made of glass wool) and lay it (PE film upward), ( 3). The laying surface is needle-punched non-woven fabric.
[0017] 2. Press molding. A 300-ton hydraulic forming machine is used to press and form the above-mentioned layers of materials. Molding temperature: upper mold temperature: 180°C, lower mold temperature: 180°C, molding pressure: 7Mpa, molding time: 170sec;
[0018] 3. Cooling and shaping. Put the semi-finished product after pressing into the cooling fixture for cooling and shaping, cooling time: 45sec; cooling temperature: 0~30℃;
[0019] 4. Waterjet cutting. On the robot cutting system, the semi-finished products that have been cooled and shaped are subjected to waterjet cutting according...
Embodiment 2
[0022] Embodiment 2: The production process steps of GAC Toyota Yaris machine cover heat insulation pad are as follows:
[0023] 1. Paving. The laying steps are as follows: (1). First lay the base fabric as impregnated non-woven fabric (PE film upward), (2). Cut glass wool (made of glass wool) and lay it (PE film upward), ( 3). The laying surface is needle-punched non-woven fabric.
[0024] 2. Press molding. A 300-ton hydraulic forming machine is used to press and form the above-mentioned layers of materials. Molding temperature: upper mold temperature: 190°C, lower mold temperature: 190°C, molding pressure: 10Mpa, molding time: 180sec;
[0025] 3. Cooling and shaping. Put the semi-finished product after pressing into the cooling fixture for cooling and shaping, cooling time: 50sec; cooling temperature: 0~30℃;
[0026] 4. Waterjet cutting. On the robot cutting system, the semi-finished products that have been cooled and shaped are subjected to waterjet cutting according ...
Embodiment 3
[0029] Embodiment 3: The production process steps of GAC Toyota Camry machine cover heat insulation pad are as follows:
[0030] 1. Paving. The laying steps are as follows: (1). First lay the impregnated non-woven fabric (PE film upward), (2). Cut the glass wool and place it (PE film upward) on the impregnated non-woven fabric, (3). The needle-punched non-woven fabric is laid on the cotton.
[0031] 2. Press molding. A 300-ton hydraulic forming machine is used to press and form the above-mentioned layers of materials. Molding temperature: upper mold temperature: 200°C, lower mold temperature: 200°C, molding pressure: 12Mpa (forming belt punching, not cutting with water jet), molding time: 190sec;
[0032] 3. Cooling and shaping. Put the semi-finished product after pressing into the cooling fixture for cooling and shaping, cooling time: 48sec; cooling temperature: 0~30℃;
[0033] 4. Waterjet cutting: waterjet cutting the semi-finished product after cooling and shaping, cut...
PUM
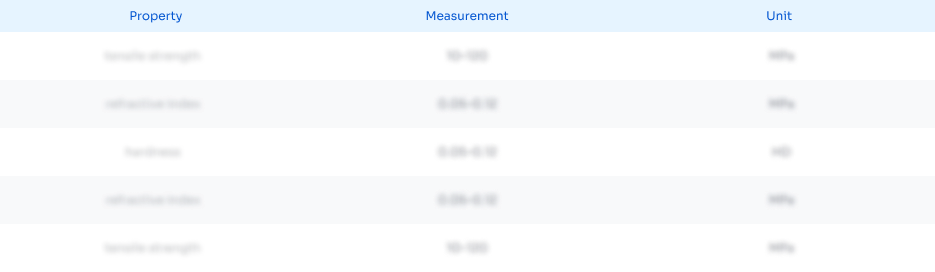
Abstract
Description
Claims
Application Information

- R&D
- Intellectual Property
- Life Sciences
- Materials
- Tech Scout
- Unparalleled Data Quality
- Higher Quality Content
- 60% Fewer Hallucinations
Browse by: Latest US Patents, China's latest patents, Technical Efficacy Thesaurus, Application Domain, Technology Topic, Popular Technical Reports.
© 2025 PatSnap. All rights reserved.Legal|Privacy policy|Modern Slavery Act Transparency Statement|Sitemap|About US| Contact US: help@patsnap.com