Coking, absorbing and stabilizing energy-saving process
A technology with stable absorption and advanced technology, which is applied in the petroleum industry, processing of gas mixtures, and treatment of hydrocarbon oil, etc. It can solve the problems of large energy loss, achieve the effects of reducing energy consumption, reducing the amount of desorbed gas, and alleviating the load in the tower
- Summary
- Abstract
- Description
- Claims
- Application Information
AI Technical Summary
Problems solved by technology
Method used
Image
Examples
Embodiment 1
[0017] Taking an oil refinery with a coking processing capacity of 400,000 tons / year as an example for simulation, the compressed rich gas volume is 4900kg / h, and the naphtha flow rate is 8300kg / h. The compressed rich gas 1, the rich absorption oil 5 from the bottom of the absorption tower 10, and the desorbed gas 6 from the top of the desorption tower 11 respectively enter the bottom, top and middle of the fluid contact heat exchange tower 9 for contact heat exchange. The top operating temperature of the contact heat exchange tower 9 is 39°C, the operating pressure is 1400kpa, the operating temperature at the bottom of the tower is 56°C, and the operating pressure is 1440kpa, and the tower top gas phase 8 obtained by the fluid contact heat exchange tower 9 all enters the absorption tower as an inlet The liquid phase 7 at the bottom of the tower is divided into two streams, one is cooled to 40°C by the condenser 13, and enters the top of the desorption tower as a cold feed, and...
Embodiment 2
[0024] Taking an oil refinery with a coking processing capacity of 400,000 tons / year as an example for simulation, the compressed rich gas volume is 4900kg / h, and the naphtha flow rate is 8300kg / h. The compressed rich gas 1, the rich absorption oil 5 from the bottom of the absorption tower 10, and the desorbed gas 6 from the top of the desorption tower 11 respectively enter the bottom, top and middle of the fluid contact heat exchange tower 9 for contact heat exchange. The operating temperature at the top of the contact heat exchange tower 9 is 39.5°C, the operating pressure is 1400kpa, the operating temperature at the bottom of the tower is 56.5°C, and the operating pressure is 1440kpa. The tower top gas phase 8 obtained by the fluid contact heat exchange tower 9 all enters the absorption tower as a The liquid phase 7 at the bottom of the tower is divided into two streams, one is cooled to 40°C by the condenser 13, and enters the top of the desorption tower as a cold feed, and...
Embodiment 3
[0029] Taking an oil refinery with a coking processing capacity of 400,000 tons / year as an example for simulation, the compressed rich gas volume is 4900kg / h, and the naphtha flow rate is 8300kg / h. The compressed rich gas 1, the rich absorption oil 5 from the bottom of the absorption tower 10, and the desorbed gas 6 from the top of the desorption tower 11 respectively enter the bottom, top and middle of the fluid contact heat exchange tower 9 for contact heat exchange. The operating temperature at the top of the contact heat exchange tower 9 is 38.5°C, the operating pressure is 1400kpa, the operating temperature at the bottom of the tower is 55.5°C, and the operating pressure is 1440kpa. The tower top gas phase 8 obtained by the fluid contact heat exchange tower 9 all enters the absorption tower as a The liquid phase 7 at the bottom of the tower is divided into two streams, one is cooled to 40°C by the condenser 13, and enters the top of the desorption tower as a cold feed, and...
PUM
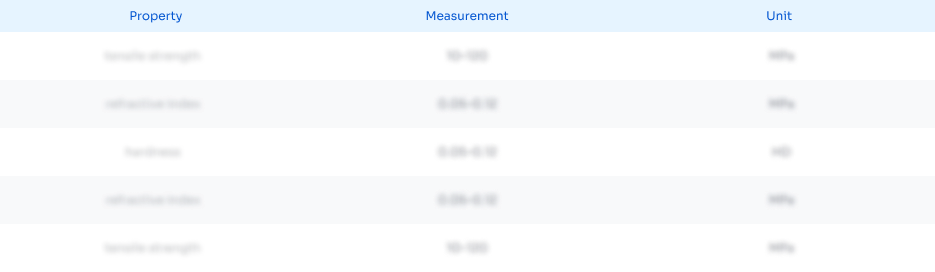
Abstract
Description
Claims
Application Information

- Generate Ideas
- Intellectual Property
- Life Sciences
- Materials
- Tech Scout
- Unparalleled Data Quality
- Higher Quality Content
- 60% Fewer Hallucinations
Browse by: Latest US Patents, China's latest patents, Technical Efficacy Thesaurus, Application Domain, Technology Topic, Popular Technical Reports.
© 2025 PatSnap. All rights reserved.Legal|Privacy policy|Modern Slavery Act Transparency Statement|Sitemap|About US| Contact US: help@patsnap.com