Disperse dye
A technology of disperse dyes and dye monomers, applied in organic dyes, dyeing methods, textiles and papermaking, etc., can solve the problems of long use time, inability to adapt to fast dyeing, poor coloring rate at low temperature, etc., and achieve a flat coloring curve , good leveling and lifting properties, excellent fastness performance
- Summary
- Abstract
- Description
- Claims
- Application Information
AI Technical Summary
Problems solved by technology
Method used
Image
Examples
Embodiment 1~6
[0027] According to the data shown in Table 1, dye monomer A, dye monomer B, dye monomer C, dye monomer D, auxiliary agent (dispersant methylnaphthalenesulfonic acid formaldehyde condensate (MF) or diffusing agent benzylnaphthalene Sulfonate formaldehyde condensate (CNF) or diffusing agent naphthalenesulfonate formaldehyde condensate (NNO) or sodium lignin sulfonate) is added with water, blended and beaten, then ground and dispersed with a sand mill, then spray-dried and packaged.
[0028] Table 1
[0029] Example name
Embodiment 7~10
[0031] According to the data shown in Table 2, monomer A commercial dye (commercial dye, monomer A content about 55%), monomer B commercial dye (commercial dye, monomer B content about 42%), dye monomer C commercial dye ( content about 60%), dye monomer D commercial dyes (content about 50%), additives (dispersant methylnaphthalenesulfonic acid formaldehyde condensate (MF), diffusing agent naphthalenesulfonic acid formaldehyde condensate (NNO), lignin Sodium sulfonate) directly blended.
[0032] Table 2
[0033]
Embodiment 11
[0035] Each 1 gram of the disperse dyes prepared in Examples 1 to 10 was dispersed in 500 milliliters of water, mixed with 180 milliliters of water after absorbing 20 milliliters, prepared 10 times and put into 10 dye vats, adjusted with acetic acid and sodium acetate buffer solution. The pH of the dyeing bath is 5-5.5. At the same time, 1 gram of polyester fiber is put in for dyeing, and the temperature is raised from room temperature to 130° C. within 90 minutes, and the temperature is kept for 20 minutes. During this heating process, take a dye vat every 10°C from 50-130°C to test the residual absorbance of the dye solution, and take a dye vat every 10 minutes above 130°C to test the residual absorbance of the dye solution. The test results are shown in the figure below :
[0036] temperature(℃)
PUM
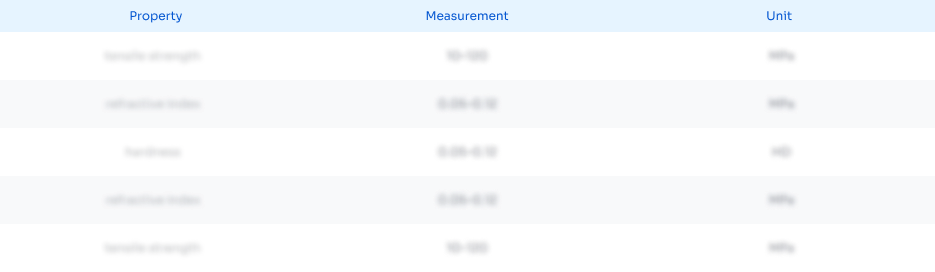
Abstract
Description
Claims
Application Information

- R&D
- Intellectual Property
- Life Sciences
- Materials
- Tech Scout
- Unparalleled Data Quality
- Higher Quality Content
- 60% Fewer Hallucinations
Browse by: Latest US Patents, China's latest patents, Technical Efficacy Thesaurus, Application Domain, Technology Topic, Popular Technical Reports.
© 2025 PatSnap. All rights reserved.Legal|Privacy policy|Modern Slavery Act Transparency Statement|Sitemap|About US| Contact US: help@patsnap.com