Preparing method of silicon viscosity reducer for drilling fluid
A technology of viscosity reducer and drilling fluid, which is applied in the field of preparation of silicon viscosity reducer for drilling fluid, which can solve the problems of silicon viscosity reducer's weak high temperature resistance and poor compatibility, and achieve high temperature resistance stability and compatibility Strong, well diluted effect
- Summary
- Abstract
- Description
- Claims
- Application Information
AI Technical Summary
Problems solved by technology
Method used
Examples
Embodiment Construction
[0007] The invention discloses a preparation method of a silicon viscosity reducer for drilling fluids, which comprises the following steps: step one, adding an appropriate amount of water into a reaction kettle, then adding methylchlorosilane, and then performing a stirring reaction to generate a mixed solution After the reaction is completed, the mixed solution is cooled; step two; after cooling, an alkali solution is added to the reaction solution to fully react, and after the reaction, aluminum sulfate solution is added to stir the reaction for 4 hours to form a silicon viscosity reducer for drilling fluid. The silicone viscosity reducer for liquid is a colorless, transparent or light yellow liquid with a PH value of 13-14 and a specific gravity of 1.1-1.3.
PUM
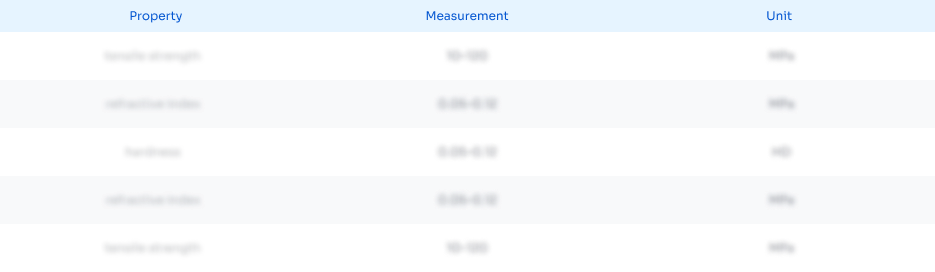
Abstract
Description
Claims
Application Information

- R&D
- Intellectual Property
- Life Sciences
- Materials
- Tech Scout
- Unparalleled Data Quality
- Higher Quality Content
- 60% Fewer Hallucinations
Browse by: Latest US Patents, China's latest patents, Technical Efficacy Thesaurus, Application Domain, Technology Topic, Popular Technical Reports.
© 2025 PatSnap. All rights reserved.Legal|Privacy policy|Modern Slavery Act Transparency Statement|Sitemap|About US| Contact US: help@patsnap.com