Technique for producing synthetic ammonia gas by inputting nitrogen-rich air into two-stage converter in membrane method
A two-stage reforming and air input technology, which is used in the field of hydrocarbon steam reforming to achieve the effects of reducing combustion, improving operating flexibility and improving fuel utilization.
- Summary
- Abstract
- Description
- Claims
- Application Information
AI Technical Summary
Problems solved by technology
Method used
Image
Examples
Embodiment 1
[0018] Use the four-stage air compressor 1 to pressurize the process air step by step to 3.49Mpa(g), use the gas-liquid separation tank to separate the liquid produced by each stage of compression, and use the interstage cooler to cool the air to 153? , the flow rate and composition of the compressed air are shown in Table 1 below:
[0019] components
N 2
O 2
Ar
Dry basis composition / %
78.10
20.95
0.95
[0020] When nitrogen-enriched air is not used, all the compressed air is directly preheated to 484° C. by the air preheater 5 and then enters the secondary reformer 6 . Another feed to the secondary reformer is the process gas from the primary reformer, with a temperature of 822°C, a pressure of 3.20Mpa(g), and a flow rate of 4200.65kmol / h. The composition is shown in Table 2 below:
[0021] components
CH 4
N 2
H 2
Ar
CO 2
CO
Dry basis composition / %
...
Embodiment 2
[0027] Use the four-stage air compressor 1 to pressurize the process air to 3.49Mpa(g) step by step, use the gas-liquid separation tank to separate the liquid produced by each stage of compression, and use the interstage cooler to cool the air to 153°C. Then part of the compressed air is adjusted to a temperature of 40°C through the cooler 2, and after impurities are removed by the precision filter 3, it enters the hollow fiber oxygen nitrogen membrane separator 4. Since the oxygen in the compressed air is preferentially permeated in the polymer membrane material, oxygen-enriched air is obtained on the permeate side of the membrane separator, and nitrogen-enriched air is obtained on the retentate side. After being separated by the membrane separator, the nitrogen-enriched air concentration on the retentate side is about 80% (mole fraction, the same below), and the oxygen-enriched air concentration on the permeate side is about 30%. The oxygen-enriched air obtained from the per...
Embodiment 3
[0032] Use the four-stage air compressor 1 to pressurize the process air to 3.49Mpa(g) step by step, use the gas-liquid separation tank to separate the liquid produced by each stage of compression, and use the interstage cooler to cool the air to 153°C. Then let part of the compressed air go through the cooler 2 to adjust the temperature to 40°C, and then enter the hollow fiber oxygen nitrogen membrane separator 4 after the precision filter 3 removes impurities. Since the oxygen in the compressed air is preferentially permeated in the polymer membrane material, oxygen-enriched air is obtained on the permeate side of the membrane separator, and nitrogen-enriched air is obtained on the retentate side. After being separated by the membrane separator, the nitrogen-enriched air concentration on the retentate side is about 90% (mole fraction, the same below), and the oxygen-enriched air concentration on the permeate side is about 28%. The oxygen-enriched air obtained from the permea...
PUM
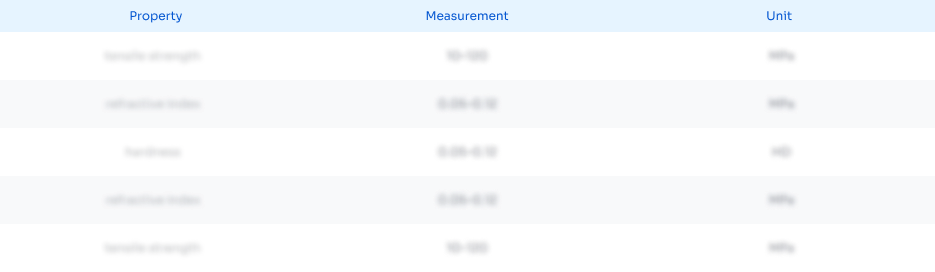
Abstract
Description
Claims
Application Information

- R&D
- Intellectual Property
- Life Sciences
- Materials
- Tech Scout
- Unparalleled Data Quality
- Higher Quality Content
- 60% Fewer Hallucinations
Browse by: Latest US Patents, China's latest patents, Technical Efficacy Thesaurus, Application Domain, Technology Topic, Popular Technical Reports.
© 2025 PatSnap. All rights reserved.Legal|Privacy policy|Modern Slavery Act Transparency Statement|Sitemap|About US| Contact US: help@patsnap.com