Three-dimensional force sensor
A sensor and three-dimensional force technology, applied in the application field of sensor technology, can solve the problems of structural design, calculation principle and complex manufacturing, design principle and processing technology, and difficult robot three-dimensional force detection, etc., to achieve light weight, simple structure, The effect of convenient processing
- Summary
- Abstract
- Description
- Claims
- Application Information
AI Technical Summary
Problems solved by technology
Method used
Image
Examples
Embodiment Construction
[0017] Below in conjunction with accompanying drawing and specific embodiment the present invention is described in further detail:
[0018] to combine Figure 1-2 , this embodiment is a cuboid structure 1, and the length of the cuboid structure 1 is L x , the width is L y , the height is L z , with 4 sides A, B, C and D arranged clockwise (or counterclockwise) in the direction of the central axis; the sides A, B, C and D respectively have cutting grooves S parallel to the force-bearing surface E A , S B , S C and S D ; The cutting groove S A , S B , S C and S D Arranged clockwise (or counterclockwise) in the direction of the central axis, and one turn clockwise (or counterclockwise) in the direction of the central axis is a cutting unit, and the distribution length is l 1 , similarly turn n circles clockwise (or counterclockwise) in the direction of the central axis, then the distribution length is l n ; The cutting groove S A , S B , S C and S D The width of b...
PUM
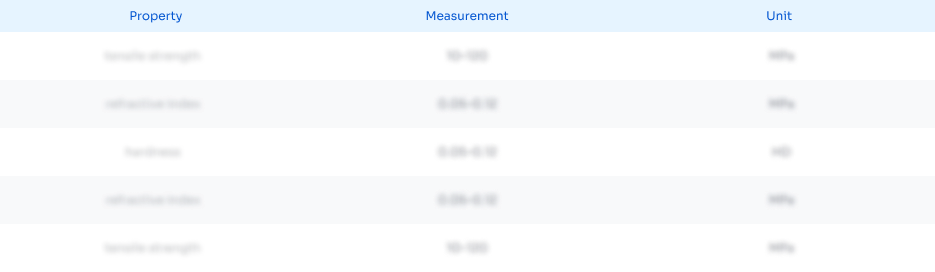
Abstract
Description
Claims
Application Information

- R&D
- Intellectual Property
- Life Sciences
- Materials
- Tech Scout
- Unparalleled Data Quality
- Higher Quality Content
- 60% Fewer Hallucinations
Browse by: Latest US Patents, China's latest patents, Technical Efficacy Thesaurus, Application Domain, Technology Topic, Popular Technical Reports.
© 2025 PatSnap. All rights reserved.Legal|Privacy policy|Modern Slavery Act Transparency Statement|Sitemap|About US| Contact US: help@patsnap.com