Spiral material quick auto transferring device
An automatic transfer, spiral technology, applied in the direction of furnace, furnace type, heat treatment equipment, etc., can solve the problems of high failure rate of parts, short life of mesh belt, impact of mesh belt, etc., and achieve the effect of reducing the failure rate
- Summary
- Abstract
- Description
- Claims
- Application Information
AI Technical Summary
Problems solved by technology
Method used
Image
Examples
Embodiment Construction
[0016] A specific embodiment adopting the technical solution of the present invention will be listed below in conjunction with the accompanying drawings.
[0017] like figure 1 As shown in the material transfer device, the transfer device is for the heating furnace 1 above, and the heating furnace 1 has a discharge port 11, and the material guide cylinder 2 is connected below the discharge port 11. For the convenience of manufacture and installation, the material guiding cylinder 2 is arranged into upper and lower parts, and the upper and lower parts of the material guiding cylinder 2 are connected through a flange 8 which is completely airtight and smoothly transitioned. As shown in the figure, the upper material guide cylinder 2 is installed in the heating chamber of the heating furnace 1 . The lower part is located outside the furnace. The material guiding cylinder 2 itself is arranged vertically up and down. The material guide cylinder 2 specifically includes an outer c...
PUM
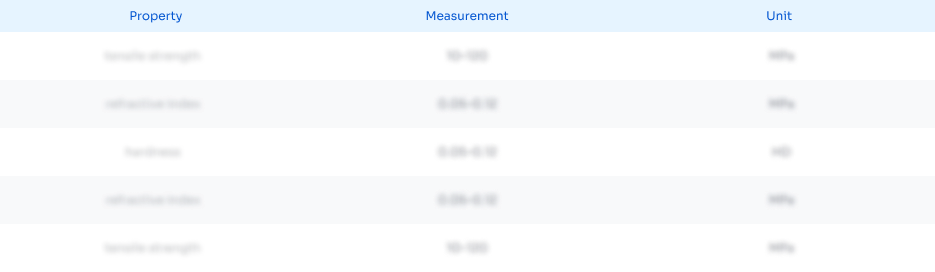
Abstract
Description
Claims
Application Information

- R&D Engineer
- R&D Manager
- IP Professional
- Industry Leading Data Capabilities
- Powerful AI technology
- Patent DNA Extraction
Browse by: Latest US Patents, China's latest patents, Technical Efficacy Thesaurus, Application Domain, Technology Topic.
© 2024 PatSnap. All rights reserved.Legal|Privacy policy|Modern Slavery Act Transparency Statement|Sitemap