Flue gas system for unbalance control of flue gas flow
A flue gas flow and unbalanced technology, applied in the field of flue gas system, can solve the problems of low-temperature corrosion and clogging, air preheater low-temperature corrosion, boiler thermal efficiency reduction, etc., to solve low-temperature corrosion and clogging, and prevent low-temperature corrosion and dust blocking, improve the effect of safety and economy
- Summary
- Abstract
- Description
- Claims
- Application Information
AI Technical Summary
Problems solved by technology
Method used
Image
Examples
Embodiment 1
[0028] Example 1: see figure 1 , this embodiment includes an air preheater 1, an air preheater outlet flue 2 and an air preheater inlet flue 3 that communicate with the air preheater 1, and the air preheater inlet flue 3 is provided with A partition plate 4, which divides the air preheater inlet flue 3 into two small flue gas passages with equal flow areas, and the small flue gas passage at the lower end of the air preheater flue gas passage is also An adjustment door 13 is provided. In this embodiment, a partition plate 4 and a regulating door 13 are newly added to the original flue gas system, so that the flue gas is divided into two small flue gas channels before entering the air preheater. The regulating door 13 in the air passage can adjust the flue gas flow of the two small flue gas passages according to the operation needs, while effectively preventing low-temperature corrosion and ash blocking of the air preheater, and reducing the exhaust gas temperature of the boile...
Embodiment 2
[0029] Example 2, see figure 2 , the partition plate 4 of this embodiment is installed at the upper end of the deflection according to the direction of the air preheater, and divides the original flue into two small flue gas channels with different flow areas, and is located at the lower end of the air preheater flue gas channel The small flue gas channel flow section is relatively large. Other connections are the same as in Embodiment 1.
Embodiment 3
[0030] Embodiment 3: see image 3 In this embodiment, the position of the partition plate 4 is biased towards the small flue gas channel at the lower end according to the direction of the air preheater, and the original flue is divided into two small flue channels with different flow areas. The flow section of the small flue gas channel at the lower end of the gas channel is relatively small. Other connections are the same as in Embodiment 1.
PUM
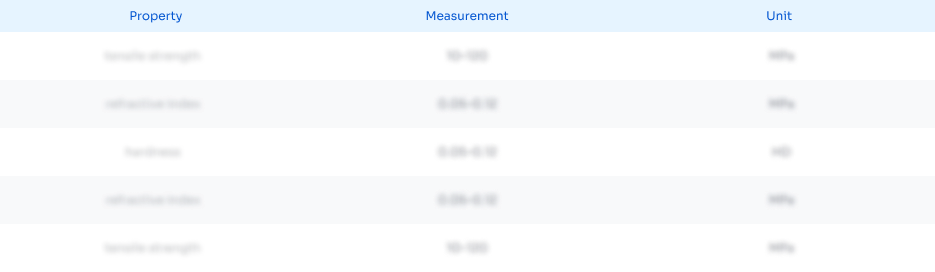
Abstract
Description
Claims
Application Information

- R&D
- Intellectual Property
- Life Sciences
- Materials
- Tech Scout
- Unparalleled Data Quality
- Higher Quality Content
- 60% Fewer Hallucinations
Browse by: Latest US Patents, China's latest patents, Technical Efficacy Thesaurus, Application Domain, Technology Topic, Popular Technical Reports.
© 2025 PatSnap. All rights reserved.Legal|Privacy policy|Modern Slavery Act Transparency Statement|Sitemap|About US| Contact US: help@patsnap.com